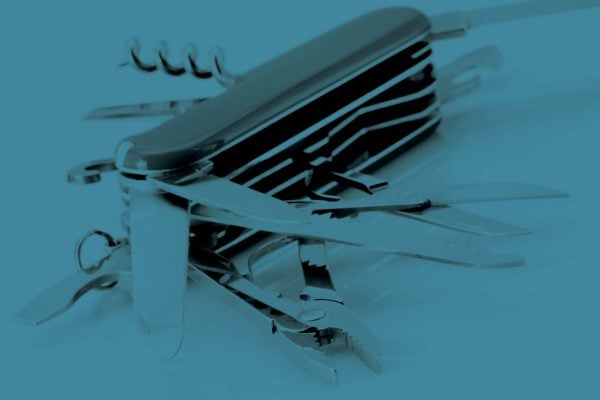
Quality
The Swiss Army Knife of Manufacturing
June 22, 2020
Whether it’s your kid’s bedroom walls or the wooden fence enclosing the back yard, a fresh coat of paint makes most things look better. What’s more, paint preserves and protects whatever it’s applied to, preventing or at least delaying the inevitable decay or corrosion that comes with time and exposure to the elements. This quality is especially true with objects made of steel and iron, where rain, snow, sun, and air will cause corrosion and eventually bring substantial deterioration to even the strongest bridge or tallest tower.
Unless that is, they’re painted. This need to protect bare metal is why the Eiffel Tower has received 60 tons of paint every seven or so years since its unveiling in 1889, and why a crew of exceedingly brave workers continuously touches up the “International Orange” paint job covering the Golden Gate Bridge at a cost of $300,000 annually.
Of course, some metals don’t need such protection. Aluminum, most stainless steels, copper and brass, superalloys like titanium, Inconel, and cobalt chrome (CoCr) alloys—these and other metals contain low to no iron, the element that reacts with oxygen to form rust. And yet, even the metals just listed will oxidize and grow ugly over time, so even if they don’t eventually fail like their iron-bearing cousins, a little beautification in the form of paint might be desirable.
Let’s start with the first one. Unlike the acrylics and watercolors you might have experimented with in grade school art class, industrial painting falls into two broad categories—wet or dry. The latter of these is known as powder coating, a process that was invented in 1945 but didn’t become popular until the early 70s, when concerns over the volatile organic compounds (VOCs) found in wet paints along with several technology advancements made dry paint (i.e., powder coat) a more attractive option.
It works by spraying colored paint powder the consistency of flour onto an electrically-grounded metal surface. This sounds easy but requires a special paint gun, to which a compressed air line is attached. As the paint particles pass through the gun, they receive a high-voltage electrostatic charge that makes them adhere to the oppositely-charged workpiece. Once the surface has been completely coated, the part is then placed in a hot oven for 10 to 20 minutes, during which the polymer-based powder melts, forming a strong, permanent bond.
Anyone who’s painted a room in their home knows that wet paint is much simpler to apply.
You’re probably familiar with using a paint brush or roller when painting inside, and you might opt for a paint gun when painting outside. Custom parts are also more often sprayed with wet paint using an industrial paint gun, but unlike with powder, there is no electric charge. As with home painting projects, a primer is usually used to improve adhesion, but there’s no need to bake wet-painted parts, although depending on the application, some might go to a very warm, very clean chamber for post-paint curing.
Whatever the process, masking might also be needed. This can be done to keep threaded holes free of paint, to leave certain areas bare for electrical purposes, and to prevent overspray onto previously painted or plated areas. As with creating a series of stripes on the bedroom wall, there’s no magic involved here, only masking tape, maybe some plastic wrap, and a very steady hand. In addition, plugs or caps can be used to preserve bare threaded holes.
Before diving into the pros and cons of each process, it’s important to note that both offer various textures and sheens. The latter can range from a flat matte finish to one that’s glossy like a sports car, while surface textures such as sand, wrinkle, veined, and so-called hammertone are commonly available. So is the proverbial rainbow of colors, with most providers (Prismier included) offering color matching as well as the choice of Pantone, Sherwin Williams, and other standard color and gloss selections.
However, powder coat’s greater thickness can be a disadvantage. Attempting to apply a thin layer can lead to a bumpy orange peel effect. And despite it being both easier and faster, the spraying equipment and gargantuan oven are a significant investment, putting powder coating out of financial reach for smaller manufacturers.
The oven just mentioned presents another challenge, in that delicate parts or those containing electronic or polymer components might not withstand the heat. Not so with traditional wet paint. Nor are there concerns over very thin layers, although multiple coats are usually necessary, as is a higher skill level with the paint gun. Wet paint is also easier to color match, however, and provides a wider range of standard colors, although there’s no shortage of options with either.
As for cost, they’re close, and any price differences are secondary to durability—if it were possible to powder coat the Eiffel Tower or Golden Gate Bridge, you can be sure those responsible for maintenance would jump at the opportunity. Prismier would have to no-quote a job like that, but we’re well-equipped to paint or powder coat parts the size of a pickup truck and smaller, and have the experience to help you decide which finishing option is the best choice for your particular project. Give us a call and we’ll get started.
If you'd like to know more, pick up the phone and call us at (630) 592-4515 or email us at sales@prismier.com. Or if you're ready for a quote, email quotes@prismier.com. We'll be happy to discuss your options.