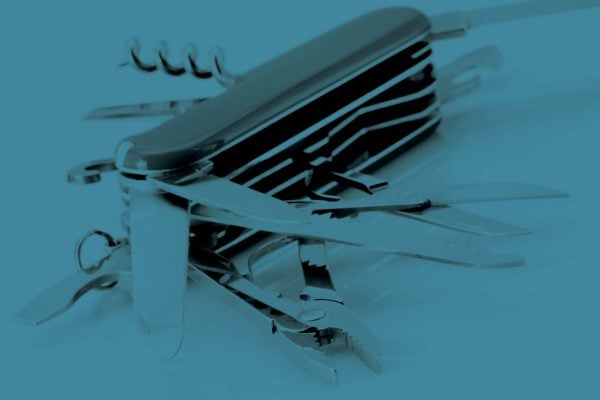
Quality
The Swiss Army Knife of Manufacturing
June 22, 2020
In the recent blog post Materials Monday: The Big Picture, we noted that aluminum is the “darling of aircraft manufacturers and cookware producers alike.” The reason is clear. Aluminum alloys in all their many forms are strong, lightweight, and corrosion resistant, attributes that make it the perfect metal for a huge variety of applications.
You already know that soda cans are made of aluminum, but so are many skyscraper parts, high-tension electrical wires, various car and truck components, as well as the hulls of an increasing number of seagoing vessels. In addition, aluminum is used in many electronic components, both at the board level, such as for the heat sink pictured at the top of this page, and for the housing enclosures that contain such components. In fact, aluminum is the world’s second-most used metal, after iron (primarily used in making steel). Approximately 63 million tons of aluminum are mined each year and combined with other industrial metals to produce a variety of alloys.
Aluminum is not so easy to extract, despite the fact that it’s the most abundant metallic element on Earth. First discovered in 1825, it wasn’t produced at industrial levels until the invention of the Hall Héroult process in 1886, which converts the aluminum oxide found in bauxite ore into pure aluminum. So important was this discovery that co-inventor Charles Hall later went on to form the Pittsburgh Reduction Company, known today as Alcoa. Today most aluminum is mined in China, Russia, and Canada, followed by the US, Australia, India and Brazil.
Manufacturing geeks and those wishing for some late-night reading can find all the mind-numbing details by cruising over to the websites of The Aluminum Association, ASTM International (formerly known as American Society for Testing and Materials), and SAE International (formerly known as the Society of Automotive Engineers). There’s also ESAB, a manufacturer of welding and cutting systems, which has some excellent educational information available in the ESAB Knowledge Center.
The aforementioned organizations are great for reference materials and research, however, there may be some costs associated with certain resources. So, unless you’re a metallurgist, the chances are excellent that your favorite sheet metal fabricator, machine shop, or die casting house (quick self-serving plug: Prismier offers all three of these services) can provide the information needed to guide you to the correct material for your current project.
That’s but a small sampling of the 500 or so recognized aluminum alloys, with more being developed each year. Nor does it discuss the various die casting alloys that are available, although the ones just listed—along with their different tempers and shapes—comprise the lion’s share of all commercial and industrial uses. As mentioned, Prismier machines, bends, forms, stamps, laser cuts, and die-casts all types of aluminum components, and stands ready to help out on your next prototyping or large-scale production project. So, if you want to talk aluminum (or any other metal), give us a shout.
If you'd like to know more, pick up the phone and call us at (630) 592-4515 or email us at sales@prismier.com. Or if you're ready for a quote, email quotes@prismier.com. We'll be happy to discuss your options.