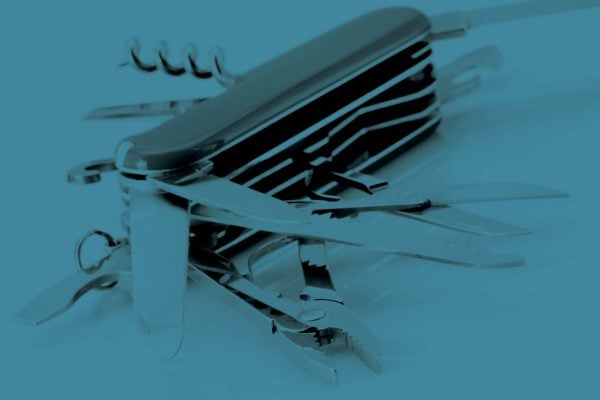
Quality
The Swiss Army Knife of Manufacturing
June 22, 2020
A NASA space shuttle, Tesla’s Model S, the newest iPhone, a fidget toy — what do all of these products have in common? They all started with a deliberate prototyping phase. Engineers often undervalue the number of iterations, effort, and time that goes into a successful prototype run.
For better results during your upcoming prototyping phase, you might consider rapid prototype manufacturing.
Rapid prototype manufacturing can create production-caliber prototypes, saving more time with each iteration you have to go through. Remember, without a production-caliber prototype in your hands, you’ll never have the full story.
In this guide, you’ll learn what rapid prototype manufacturing is, some real-world examples, and 8 benefits of using this manufacturing method for your next product development project. Let’s get started with a quick definition.
Rapid prototype manufacturing is a method of creating physical parts quickly and affordably. These parts are made out of high-quality material — usually metals or plastics — allowing you to learn a ton about your design.
The key word is “rapid”. There are a hundred ways to make a part, but very few methods when it comes to making high-quality prototypes very quickly.
Compared to other manufacturing methods, 3D printing allows manufacturing partners like Prismier to create parts:
We can even print multiple iterations of the same prototype at the same time, allowing you to try different configurations of your design simultaneously.
As you might know, designing and prototyping a part is the first step of any product development workflow. Want to make the next big product? No matter how many hours you spend on CAD, you’ll need at least one physical iteration of your prototype if you want to have success.
The purpose of a prototype is to fine-tune your design and optimize your direction by manufacturing a few parts before you commit to a full-scale production run.
Making prototypes out of stock metal can get expensive, and it gets painful when you spot an issue and have to scrap the part. This is another reason why plastic 3D printing is the preferred method for rapid prototype manufacturing — it’s a lot quicker and less expensive.
The term “rapid prototype manufacturing” is outdated and can theoretically apply to many different manufacturing methods, but 99% of the time it refers to 3D printing.
Metal 3D printers (DMLS), urethane casting, rapid injection molding, and CNC machining are options for making prototypes too, but they are very infrequently thought of when you mention rapid prototype manufacturing. Still, Prismier can help with any and all manufacturing methods you ultimately choose.
There are other ways to prototype a product, but what makes rapid prototype manufacturing so perfect? There are plenty of benefits:
1: Quick Fitments and Functionality Tests
One of the best things about a physical prototype is that you can touch it, manipulate it, and move it around. If your product is supposed to fit into an existing assembly or machine, a rapid prototype will make sure all of your measurements and dimensions are perfect — you can put the physical prototype into the assembly and see if it fits or not.
Not to mention, a fitment test with a CNC-machined prototype will show you what kind of tolerances you should consider for your full-scale production run. If you don’t have a ton of wiggle room, then you’ll need to tighten up your tolerances — that’s a great thing to discover before placing a massive manufacturing order.
2: Save Time and Money by Spotting Issues Early
When it comes to any product development cycle, you’ll save exponentially more time and money when you change your design prior to starting a full production run.
Take an injection-molded toothbrush, for instance. Without a prototyping phase, you might spend tens of thousands of dollars and waste months of your time creating the tooling, only to find out the handle is too large and it’s uncomfortable to hold. At this point, it’s too late to change anything. Unfortunately, your company just wasted time and money on a design that won’t work. Alternatively, you can spend less than $300 and a few days to get a rapid prototype manufactured and learn the same lesson.
Spotting an issue early can prevent massive disasters, and that’s why rapid prototype manufacturing is invaluable.
3: Optimize Your Product Development Cycle
As we mentioned, every product development cycle should include a prototyping phase. By opting for rapid prototype fabrication, you’ll save a lot of time during this crucial first step, while getting the same amount of valuable feedback.
With 3D printing specifically, you can save days, weeks, or months in your total prototyping phase. It becomes even more impactful when you have the help of a high-quality manufacturing partner like Prismier.
Pro Tip: A full-scale manufacturer can also provide insights into DFM. Our team at Prismier will utilize their knowledge and hands-on experience to make suggestions that will help minimize iterations, keep your costs lower, and expedite every build.
4: Stakeholders (and Marketing Teams) Love Physical Prototypes
It seems silly, but it’s incredibly true: stakeholders, investors, and potential customers love to touch a physical product before making their decision. Pictures on a screen or a big posterboard are nice, but they pale in comparison to a tangible object, whether it’s a 3D-printed, CNC-machined, Urethane-molded, or rapid injection-molded part.
If a picture is worth a thousand words, a physical prototype is worth a few million.
A rapid prototype might be the difference between getting a deal from investors, and a product that fails. It’s like going to the bank to make a deposit with a picture of money — you’ll get a lot more out of the process if you have the physical goods, instead.
5: Try Different Designs to Find the Right Option
With 3D-printed prototypes, you have the opportunity to test a dozen different setups and configurations at the same time with minimal impact on your overall timeline. If we print different versions of your part at the same time, then you can test each option and take lessons learned from every iteration.
From there, you can dial in the exact direction you want to go.
Pro Tip: Don’t rush through the prototyping phase. By trying different iterations of your design, you can find the “perfect” design of your product before you roll out full-scale production. Don’t just try iterations that you’re in love with, try a few “meh” options — you never know what the winning design will be until you make physical prototypes.
6: Have More Confidence in Your Production Design
Even though CAD has come a long way, the most experienced designers and engineers have to go through prototyping phases before they’re confident in their design. Your part might look perfect in CAD, but real-world manufacturing is a completely different beast.
With prototyping, you can boost your confidence. Doing things like destructive testing, fitment checks, and check-ins with stakeholders can ensure your product is successful. The good news is that Prismier can help with all of these tests and checks as well. Sometimes it’s helpful just to sit at your desk with a 3D-printed prototype in your hand and move it around, looking at every angle— you can spot an issue that you never thought of while your part was open in CAD.
7: Get to Market First
For any type of consumer product that you’re designing, it’s a matter of days and dollars. Making more affordable products that are available sooner is the gold standard for this industry.
With rapid prototype manufacturing, you can check off both of these boxes at once. For starters, the prototypes will be manufactured more quickly, allowing you to expedite your overall production workflow. What does that mean? It means that you can hit the shelves sooner, make OEM parts faster, deploy your new product line quicker, and start shipping units before your competitor does.
Saving time and money on each part becomes exponentially more important as you scale up. With mass production, the savings you experience through prototyping can be the difference between the failure and success of your launch.
Pro Tip: Skipping the prototyping phase in hopes of shortening the overall product timeline is never advised.
As Prismier’s co-founder says,
“Spend an extra day in design and you could save a week of costly design changes and tooling modifications. Spend an extra week in design and you could save a month of costly design changes and modifications. Spend an extra month in design and you could save a year of costly design changes and tooling modifications.”
8: Unlock a Partner for Production as Well
A high-quality fabrication team working on your prototyping needs can convert to an asset when it comes to long-term fabrication. With us, we can have a quick phone call on a whim and start producing your next project without any wasted time.
At Prismier, we have a lot of companies that approach us simply looking for a prototype. After they see the quality, turnaround time, and attention to detail in their prototype, they ask about our full-scale production abilities.
We can help with your one-off, small-batch, medium-volume, or full-scale production needs. By starting together in the prototyping phase, we already know:
The result? Better parts at better pricing.
Pro Tip: Although you can choose a manufacturing partner at any step of your product design, it’s always best to start working together sooner rather than later.
At Prismier, we’re not just a machine shop — we’re a single-source, full-service manufacturing partner. We’re here to connect the dots between a rough CAD drawing of your idea and an optimized, full-scale production run of your product. With us, it’s as simple as P.I.E.: getting Prismier Involved Early. Our team is staffed with engineers and fabrication experts, and we have access to all of the manufacturing equipment needed for your upcoming prototyping and production phases.
By choosing Prismier for your rapid prototype manufacturing, you’ll unlock speed and expertise that you won’t find elsewhere, paired with the flexibility and personability that your team deserves. Allow us to handle your manufacturing and design decisions, so you can focus on the big picture of your company. Upload your part files for a free quote today.