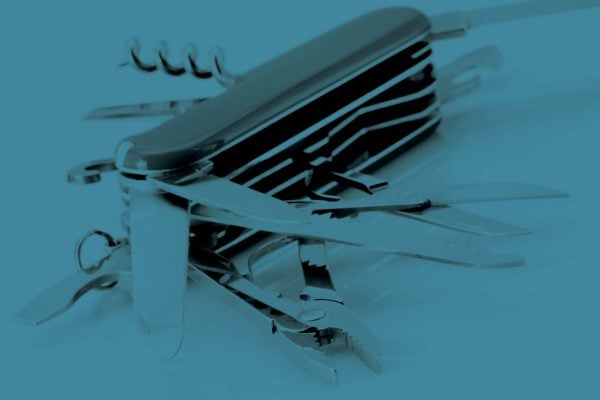
Quality
The Swiss Army Knife of Manufacturing
June 22, 2020
Though long considered a prototype and low-volume manufacturing process only, AM is quickly becoming a viable technology for many end-use and even mid-volume components. Given the right product or component, a manufacturer could use 3D printing to rapidly iterate various designs, then segue into higher volumes while their production tooling is being made, or in some cases, use AM for the entire product lifecycle. That said, many factors come into play on any design project, starting with the decision over which 3D printing process is most suitable for your application. Here’s a list of the available technology options followed by a quick overview of each:
Stereolithography is best known by its acronym SLA. Of all the commercially available additive manufacturing processes, it is the oldest—some refer to its inventor, Charles Hull, as the Father of 3D Printing. He received a patent for his “Apparatus for Production of Three-Dimensional Objects by Stereolithography” in 1984 and went on to found what is now an industry giant, 3D Systems. SLA uses a vat of photocurable resin, inside of which sits a movable platform. An ultraviolet (UV) light source situated at the top of the “build chamber” traces the outlines and interior of 3D models that have been digitally “sliced” into paper-thin layers, curing the polymer as it passes. Once each layer is complete, the platform drops down and fresh resin is applied. The process continues, building the part from the bottom up until complete.
Fused Filament Fabrication (FFF) is another old-timer in the additive world, although it is most often referred to by its trademarked name, FDM (Fused Deposition Modeling). That term came from another AM industry pioneer, Scott Crump, who was reportedly looking for a more efficient way to make a plastic frog for his daughter when he latched onto the idea of a hot glue gun, which he eventually placed under computerized control. He went on to found Stratasys, another leading 3D printer manufacturer. Whether you call it FFF or FDM, it is an extrusion process. It uses a heated nozzle to melt plastic feedstock supplied by a Weed Whacker-like reel of filament overhead. As with SLA and indeed most additive processes, parts are built one layer at a time, starting from the bottom up, and deposited onto a movable platform. Once the completed parts have been removed from this platform, they must undergo secondary operations to remove “support material” along with sanding or grinding to smooth the rough, staircase-like surfaces common with most 3D printed parts.
Digital Light Processing (DLP) uses photocurable resin similar to that found in SLA machines. Rather than tracing each layer with a thin beam of light like filling in a coloring book, however, DLP projects a complete image of each layer—think of it as frames in a movie—onto a transparent platform sitting at the bottom of the resin tank. This is said to provide significantly faster build rates than SLA, and is also one of the few AM processes that builds parts from the top down. In addition, DLP can produce soft, squishy parts similar to those made from TPU (Thermoplastic Polyurethane), while SLA and FFF are thus far limited to rigid materials like PLA, ABS, and Nylon. Carbon is one company that has built a business on the technology (they use the term Digital Light Synthesis, or DLS), although others are rapidly climbing aboard the DLP bandwagon.
Selective Laser Sintering (SLS) is one of many laser-based additive technologies but is the only one that uses plastic powder. Where SLA relies on a bed of liquid resin and UV light to build parts, SLS uses a laser beam to fuse individual polymer particles roughly the consistency of flour or fine sand. As each layer is completed, the platform descends by one layer thickness and a scraper blade drags a fresh layer of powder across the burgeoning workpiece. SLS was developed in the mid-80s by Dr. Carl Deckard and his adviser Joe Beaman at the University of Texas. The two went on to found the DTM company, which was acquired by 3D Systems in 2001. Unlike most 3D printed parts, those made with SLS require no supports, providing for more complex geometries and less secondary processing. These parts are, however, largely limited to Nylon and filled Nylon materials, although that is beginning to change with 3D Systems’ development of SLS-compatible polystyrene and elastomeric thermoplastics.
Powder Bed Fusion (PBF) is another laser sintering process but refers to parts made of metal. Due to the exciting possibilities presented by 3D printed metal parts, PBF is one of the most rapidly growing and investment-intensive of all AM technologies. As such, you’ll seldom hear it called PBF, but rather terms like Selective Laser Melting (SLM), trademarked by SLM Solutions, or Direct Metal Laser Sintering (DMLS) by EOS GmbH, or LaserCUSING from Concept Laser, now owned by GE Additive. There’s also Electron Beam Melting (EBM) by Arcam, which as its name implies, uses an electron beam rather than a laser to melt the individual particles. Each shares similarities and each manufacturer will espouse the virtues of their equipment, but unless you have a couple million bucks to invest in the equipment and software necessary to print metal parts, users should focus instead on learning about its limitations and opportunities so they can subcontract the work to a competent service bureau. Because it is a thermally intensive process, robust support structures (anchors, actually) are needed to keep parts from curling during the build process. Extensive machining is often required to remove said supports and to finish-bore holes, tap threads, and mill critical surfaces. Despite this, huge advancements have been made with this technology, including the metal implants mentioned earlier as well as the consolidation of multi-piece metal assemblies into a single, monolithic part.
Bound Metal Deposition (BMP) also uses metal powder, but only after it has been “bound” into crayon-like feedstock impregnated with a polymer binder. This material is deposited onto a build plate, after which the 3D printed parts are washed in a chemical solution to remove most of the binder before being placed into a hot oven to cure. BMP’s roots lie in the decades-old Metal Injection Molding (MIM) industry, and even use some of the same metal powders. Companies like Desktop Metals and Markforged lead the pack here, which boasts a far lower capital investment point than PBF and is much faster besides. As with other metal AM processes, it produces fully-dense parts that are well-suited for end-use applications, as well as prototyping where form, fit, and function testing is needed. Like PBF, a wide variety of materials are available, including tool steel, copper, Inconel, and various stainless steels and steel alloys.
Multi Jet Fusion, or MJF, is the darling of well-known office printer company HP Inc. It uses an inkjet array that deposits “fusing and detailing agents” across a bed of polymer powder, which are then cured with infrared light. As with SLS, Nylon is currently the most commonly used material, although HP also offers Ultrasint (a type of TPU) and its version of polypropylene (PP). Some proponents suggest that the company will begin offering electrically conductive materials, opening the door to components with integrated circuitry. Similar to MJF is Binder Jet, a technology developed by MIT and then licensed to the ExOne company, which uses it to print patterns and molds for sand casting, among other things. GE Additive is eagerly pursuing its own Binder Jet program, thanks to its reported ability to significantly increase production rates compared to competing 3D printing methods.
Though an important part of the industry overall, AM should be thought of as a complementary process, not a competing one. Even the fastest 3D printer cannot compete with the speed of a CNC machining center or press brake, and is limited in terms of part size and especially accuracy. What’s more, 3D printing requires an entirely different skillset and design principles, something that far too many manufacturers have learned to their chagrin.
The message here is clear: 3D printing has its place, but as you can see, is an immensely complex and technical subject. Anyone looking to leverage it in their next design project should first speak with subject matter experts and then balance AM’s impressive capabilities with part cost, delivery speed, product quantity, and alternative manufacturing processes. Feel free to give us at Prismier a call if you’re contemplating a move to additive. You’ll be glad you did.
If you'd like to know more, pick up the phone and call us at (630) 592-4515 or email us at sales@prismier.com. Or if you're ready for a quote, email quotes@prismier.com. We'll be happy to discuss your options.