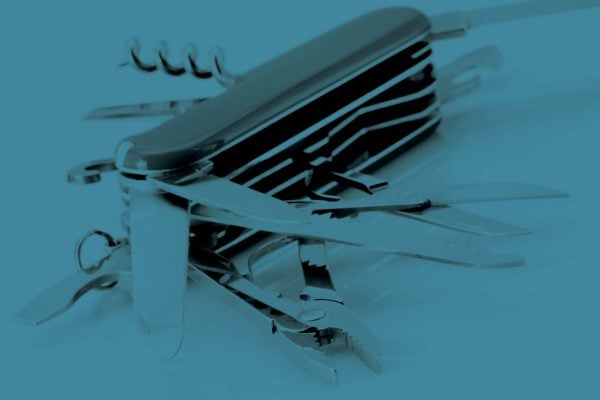
Quality
The Swiss Army Knife of Manufacturing
June 22, 2020
We’ll talk more about the various types of stamping machinery and the operations they perform in a moment, but all are equipped with a movable slide or ram, to which the top half of a die is attached. As the ram moves up and down, often at great speed, it forces a punch (or punches) within the die into and sometimes through the sheet of metal below. Forming and coining tools may also be present in the die, as well as tools used to bend, slice, or emboss the metal.
Brief descriptions of each of these operations is forthcoming, but what’s important for now is that progressive dies are generally more expensive than single-station dies, and are therefore found in high volume applications—think millions of parts, although this is not always the case. Transfer die stamping, on the other hand, uses separate dies and sometimes separate machines. With each stroke of the press or presses, the system transfers the in-process workpiece to the next station. Of course, for lower volume work, a human or team of humans can accomplish the same thing, although this would obviously not be called automated transfer stamping.
As you can see, production quantity plays a key role in determining the type of die and stamping strategy. Here’s a brief recap:
Whatever the die and however many operations it performs per stroke, all are precision-machined, typically using CNC lathes and machining centers, different types of grinding equipment, and wire or sinker EDM. Hardened tool steel is usually the material of choice for the tools themselves, which are attached to a steel die set, although harder and more expensive carbide might be used on production tooling.
The workpiece material and its final shape may also play a role in all this decision-making. For instance, stamping of hardened steels or superalloys such as Inconel and titanium would almost certainly call for carbide tooling, while a low-volume part made of mild steel could be stamped using regular tool steel. Similarly, small complex parts made in high volumes would mandate a progressive die, just as stamping out a few dozen salad bowl-shaped parts is easily accomplished via a simple die and manual loading.
So do the different drive types. Flywheel-driven mechanical presses are the oldest of all and still make up the lion’s share of presses today, and are available with a wide variety of geared transmissions. Hydraulic presses, however, provide greater control over stroke speed and can apply full tonnage throughout the stroke, an attribute to which mechanical presses cannot lay claim.
Over the past few years, electronic servo-driven presses have come on the scene. Though not yet available in the higher tonnages seen with mechanical stampers, servos are said to offer the greatest control and accuracy of all presses, with full power available anywhere in the stroke. This makes them an excellent choice for job shops, where a wide array of materials and thicknesses as well as workpiece shapes are encountered.
There’s far more. For example, cutting is the last step in a progressive die, when the completed workpiece is finally removed from the coil. Flanging creates reinforced edges around holes and workpiece perimeters. Trimming removes the wrinkled bit of leftover material around the edge of blanked parts. And, of course, stamping can also perform bending, ironing, slitting, notching, and other operations.
Admittedly, the past few pages have offered but a small taste of the metal stamping pie. Like most metalworking fabricating processes, this is a deep and highly complex technology that takes years of study and experience to master. That said, the information presented here should serve as a good foundation for anyone looking to design or purchase stamped metal parts.
If you'd like to know more, pick up the phone and call us at (630) 592-4515 or email us at sales@prismier.com. Or if you're ready for a quote, email quotes@prismier.com. We'll be happy to discuss your options.