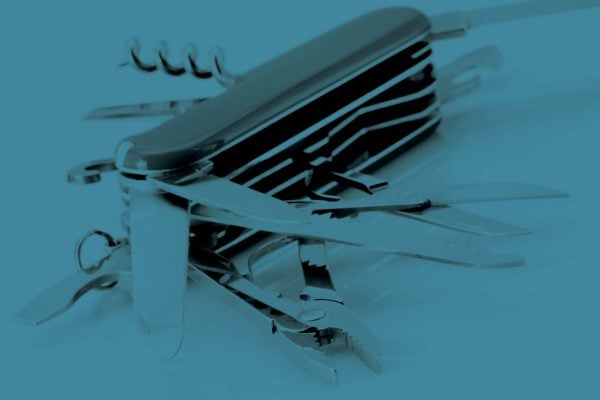
Quality
The Swiss Army Knife of Manufacturing
June 22, 2020
This technology is ideal for buyers who need between a few parts to perhaps 10,000 or more, and who want their parts in a couple weeks and with minimal investment.
What we didn’t talk about are the various types of plastic injection molding services available, how they differ from one another, and why a careful analysis of the options can spell the difference between an overwhelming success and an expensive lesson. Here are some of the alternatives to Rapid Injection Molding and their trade-offs:
A quick Google search for plastic injection molded parts illustrates an important fact: buyers of such products have plenty of options. The challenge, then, is finding a reputable shop able to produce the required number of parts within the budget, timeframe, and quality requirements said buyers can work with. And there’s the rub.
Because there are so many ways to crack the plastic injection molding nut, anyone who’s not an expert on the topic might find supplier selection challenging. Worse, those who want fully functional prototype and low to mid-volume parts quickly might make an expensive mistake. As you’ll see, RIM is often the best solution for a variety of manufacturing needs.
Of course, some of you might argue “why not just 3D-print the parts, especially if we only need a handful?” It’s a good question, but one that’s easy to answer: 3D printed parts do not have the same mechanical properties as those that have been injection-molded, and are therefore unsuitable for functional testing. With RIM, you’ll get fully production-grade parts to facilitate all your testing and troubleshooting efforts.
At Prismier, RIM begins with another acronym, MUD. It’s short for Master Unit Die, and it is to the molding industry what modular furniture is to IKEA. As the name implies, a MUD is a quick-change die system that utilizes standardized mold inserts made of P20 tool steel, a tough but readily machinable low carbon alloy.
Because the customer only pays for the inserts and not the entire mold, the up-front investment is much lower. And as already mentioned, this is a quick-change system, so setup times are significantly shorter than with traditional mold tooling, further reducing part costs. Slides and lifters are possible, as is overmolding. The only restriction is size—Prismier’s proprietary MUD system is limited to parts measuring 12″ x 12″ x 4″ high.
Because we also have sinker EDM capabilities, we’re able to generate square corners and other part features not possible with a milling cutter. This opens numerous doors on design flexibility. That said, RIM molds are not hardened like their production counterparts, so the machining process is both faster and less expensive. The result is lead-times of between 3 to 12 days, with a far lower price per piece than competing methods can offer.
If you'd like to know more, pick up the phone and call us at (630) 592-4515 or email us at sales@prismier.com. Or if you're ready for a quote, email quotes@prismier.com. We'll be happy to discuss your options.