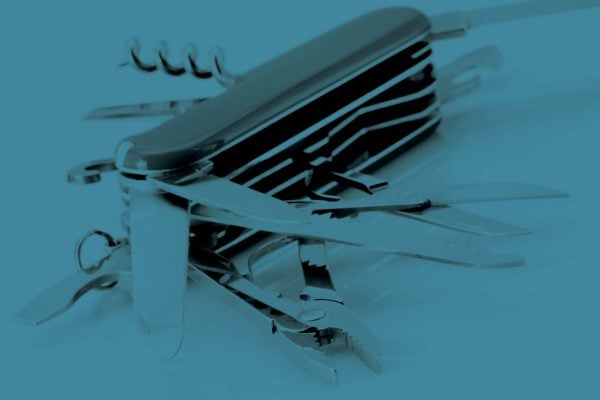
Quality
The Swiss Army Knife of Manufacturing
June 22, 2020
And of course, there's Jello molding, used to make yummy desserts for family occasions. Hold the canned fruit, please.
Because of this, plastic injection molded parts are everywhere. The mouse you hold in your hand for hours each day was injection-molded. So was your keyboard, the remote control for the TV, the little knobs on the coffee maker, the spork you used to gobble up some KFC coleslaw at lunch and the Tupperware container used to store the leftovers. It’s a seemingly endless list and will only become longer as material scientists continue to deliver stronger, more functional polymers, ones that often contain glass, carbon fiber, and other performance-enhancing additives.
Setting aside such gaming excitement, Hyatt’s invention was relatively simple, using a syringe-like device as the means to inject plastic through a heated chamber and into the mold cavity. Just after the conclusion of World War II, inventor James Watson improved on that idea with a screw-type machine. This provides greater control over injection speed and allows the introduction of additives and colorants. That basic design, though much improved upon over the years, remains in use today.
Sitting at the end of the barrel is a stationary platen, to which one half of the injection mold (the A-side) is attached. The other half is attached to a sliding press-like mechanism that clamps the two mold halves together. Once closed, a plunger forces a predetermined “shot” of hot plastic through a nozzle at the barrel’s end, through the platen and into the mold. It then travels down a series of runners and sprues and into the mold cavity proper (or more likely, multiple cavities).
Once the hot plastic has had a chance to cool slightly—often with the assistance of liquid-filled channels that run through the mold base—the movable platen holding the mold’s B-side retracts. Ejector pins within the mold give the injection-molded part (or parts) a nudge, and out pops a nearly complete kegger cup or F-18 replica. All that’s needed is to trim away the runners, remove any excess material around the gates and sprue, and possibly “de-flash” any material that seeped into the separating line between the two mold halves.
It’s even possible to “overmold” a workpiece. In this instance, a softer material is injected into the mold over the top of the part’s harder base material—the handle on your battery-powered drill, for example, might have been overmolded to give it a more ergonomic feel. In addition, metal components such as threaded inserts and bushings are often placed into the mold before the injection process. This is called insert molding, and it provides the finished part with mechanical properties unachievable using plastic alone. Simply put, plastic injection molding is a highly complex affair.
There’s lots more. Nylon (polyamide), PMMA (acrylic), PP (polypropylene), POM (polyoxymethylene). One would have to spend an entire day with a materials expert to explore all the different thermoplastics, their properties, and their uses. There’s no time for that, however, which is why we’re going to wrap up with a few design tips for those who might be considering a visit to a plastic-injection molding house.
First off, the wall thickness of any injection-molded part should be as consistent as possible. Not too thick, not too thin, and not too tall—depending on the part size, a 1/8-inch thick wall (2-3 mm) is a good rule of thumb. Sharp edges should be avoided, especially on internal corners, where stress can be a concern. The part walls will need some slight taper, or draft, to aid in ejection from the mold. Undercuts increase part cost, as do highly cosmetic surfaces, certain polymers, and parts designed without plastic injection molding in mind.
Here again, this is just an overview. Basic knowledge of these and other Design for Manufacturability (DFM) principles is an essential tool in any engineer’s toolbox, and even procurement people can benefit from knowing how parts are made and what materials should be used to make them.
If you’d like to chat more about plastic injection molding, get in touch with us. Prismier does lots of it, and we’re happy to steer you in the right direction. Until then, stay tuned for the next installment of Learn Up: What is Metal Stamping?
If you'd like to know more, pick up the phone and call us at (630) 592-4515 or email us at sales@prismier.com. Or if you're ready for a quote, email quotes@prismier.com. We'll be happy to discuss your options.