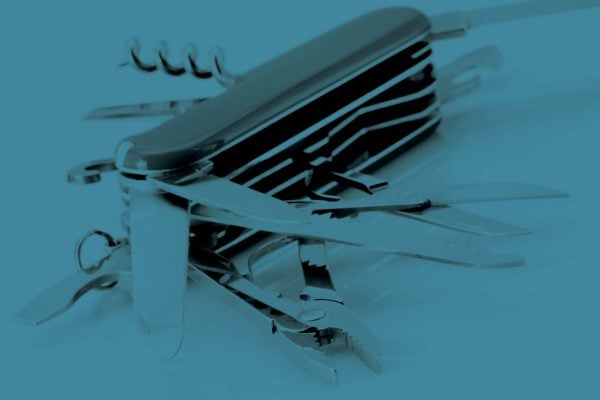
Quality
The Swiss Army Knife of Manufacturing
June 22, 2020
Press brakes use a pair of male and female tools—the punch and die—respectively. They are typically V-shaped, although a host of other shapes and angles are available. Regardless of its shape, the punch is attached to the press brakes’ movable ram—in our window example, this would be the lower sash’s bottom face. The punchs’ female counterpart—the die—sits directly below on the press brake’s fixed bolster (on the window sill, in other words).
The bending operation starts by placing a flat piece of metal—the blank—across the top of the die and against a movable back-gauge. At this point, the operator cycles the ram downwards, which then pushes the sheet metal into the die opening, bending it. Depending on the tools’ shapes and their engagement amounts, practically any angle is possible, and multiple bends can be created by moving the workpiece lengthwise down the bolster across various punch and die sets, performing one bending operation with every up-and-down cycle of the ram.
Let’s take both of those concepts one step further. Forming presses and especially stamping presses are among the most important of all precision sheet metal fabricating equipment, at least to higher-volume manufacturers. They’re similar in action to a press brake, but where brakes are generally limited to bending (some exceptions exist), presses can also form, punch, shear, and even insert hardware components. The bumpers, hood, and quarter-panels on your car are formed with a single blow from a forming press. So are soda cans (a process called deep drawing) as well as the big metal bowl you used for potato salad last weekend (although it might have been hydro-formed or even “spun” on a lathe).
However you cut precision sheet metal parts, you’ll often need to join afterward. That’s where welding comes in. It’s a deeply technical topic—and we’re only scratching the surface here—just know that multiple types of welding technologies are available, among them resistance, solid-state, electron beam, friction stir, and ultrasonic welding. Most work by A) heating two metal workpieces to sufficiently high temperatures that they begin to melt and flow together, or B) hot enough to melt a filler metal that then flows between the two, forming a permanent bond between the two.
A gas torch might be used, as can a laser beam, but the most common welding method relies on electric current. This is known as arc welding, and even here, multiple approaches exist. There’s MIG (metal inert gas) welding, TIG (tungsten inert gas), SMAW (shielded metal arc welding), and others, all of which require a skilled hand (or sophisticated robot) to accomplish. The metals must also be weldable (aluminum, stainless steel, and low carbon steel), and secondary heat-treating processes are sometimes required, as is grinding and buffing to make the welded parts pretty again.
We’re nearing the end of the manufacturing process for most sheet metal parts. Before we get to the finishing department with its paint booths and powder coating stations, let’s discuss PEM inserts. That’s a brand name for a popular line of threaded fasteners, standoffs, studs, and pins that can be installed on most any sheet metal component. If you’re designing a self-service ordering kiosk for use at fast-food restaurants, you will likely want panels that are easy to remove. This is a great use for PEM inserts which are installed on a special machine called—you guessed it—a PEM inserter.
For more permanent joining of sheet metal (aside from welding), there’s also riveting, and if the metal is thick enough, tapped holes or self-threading screws. Whatever the joining method though, chances are that you’ll want your precision sheet metal parts to look nice. Here again, there’s a rainbow of finishing methods available, each with its own benefits, limitations, and specific application variables.
A batch of stamped steel brackets might be sent out for zinc plating, for example, while laser-cut aluminum sprockets will likely get anodized. Larger parts like the kiosk panels just mentioned will often receive a coat of paint and clearcoat. For a more durable finish, powder coating might be the answer, which you can think of as dry paint that’s applied electrostatically. There’s also chromate conversion coating, cadmium, copper, and chrome plating, electroless nickel…the list goes on.
As noted in Part I of Learn Up: Precision Sheet Metal Fabrication, this is a complex, highly technical industry, and while this brief overview serves an important purpose, it’s far from complete. In future installments of Learn Up we’ll explore machining, 3D printing, and delve more deeply into specific topics such as stage tooling and flanging techniques.
If you'd like to know more, pick up the phone and call us at (630) 592-4515 or email us at sales@prismier.com. Or if you're ready for a quote, email quotes@prismier.com. We'll be happy to discuss your options.