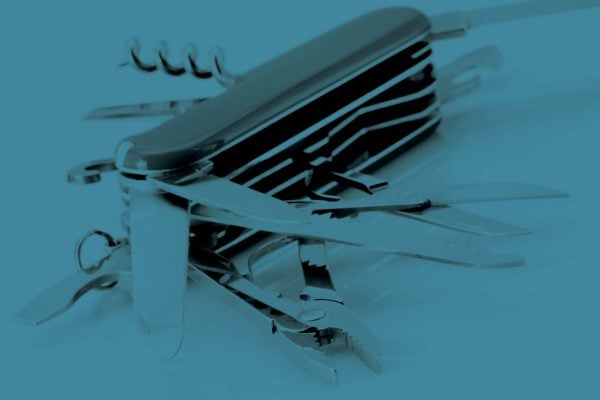
Quality
The Swiss Army Knife of Manufacturing
June 22, 2020
Everyone has to start somewhere, though, so let’s begin with the term “fabrication.” Merriam Webster defines it as “to construct from diverse and usually standardized parts.” This terse description is technically accurate, but it’s also far too vague, and could be applied just as well to IKEA furniture as it can to the modulator bracket with which you’ve been tasked. For our purposes, fabrication is the process by which skilled people cut, bend, punch, form, notch, shear, stamp, weld, and assemble sheet metal into usable shapes. Let’s start with the first of these: cutting.
As their name implies, laser cutters are equipped with a high-power laser. Two types exist—the traditional CO2 laser and the newer solid-state or fiber laser. Each has its strengths and weaknesses, although fiber lasers have largely taken over the industry due to their greater speed and lower maintenance costs. Some boast lasers of 10-kW (kilowatt) or more, with machines growing more powerful each year.
Lasers positively rock at cutting out practically any shape that fits within one of the sheet sizes just mentioned.
For thinner materials in particular, they’re much faster than competing methods, and perhaps most importantly, require none of the tooling needed on most other machine tools. All that’s needed is plenty of electrical power and a stream of “assist” gas to clear molten material from the 1/32″ wide kerf. Simply program the machine to trace out whatever part shapes are needed, load a sheet of material, and fire up the beam.
Because these tiny rocks are flying along at roughly twice the speed of sound, they’re able to rip through practically anything in their way, and that includes glass, ceramic, composites, and yes, metal. Though nearly as accurate as laser cutting, AWJ is far slower and cannot compete on the thinner gage materials that comprise the majority of all precision sheet metal parts.
Nor can plasma cutters, even though they’re significantly faster than waterjet and even lasers on certain materials. Known as the fourth state of matter, plasma is most often created by sending an electrical current through a swirling, high-speed stream of gas such as nitrogen or argon. Get that gas hot enough and it ionizes, creating plasma, which can then be used to cut steel, aluminum, and other metals up to a couple of inches thick. It’s a relatively low-cost process but its accuracy is nowhere near that of laser-cutting, so is generally used for construction, ship building, and salvage work.
This allows turret punches to generate round holes, squares, rectangles, and pretty much whatever shape has been ground into the punch and die (which must always match). By moving the sheet metal slightly with each stroke of the ram, turret punches can nibble contours within the workpiece, or even cut it out entirely from the sheet. And when used with special tooling, turret punches can also emboss shapes in the workpiece surface, or to cut and form the louvers and other shallow shapes just mentioned.
Granted, each of the preceding sections are gross oversimplifications of highly technical processes, but hopefully there was enough there to get your mental wheels turning. In the second part of “Learn Up: Precision Sheet Metal Fabrication,” we’ll cover other processes such as bending, forming, welding, hardware insertion, and assembly, but for now, let’s go back to our modular bracket.
As indicated at the outset, precision sheet metal fabrication is a deep topic, and even those with decades of experience are often left scratching their heads. For now, don’t worry about it—keep reading all you can, and don’t hesitate to give the knowledgeable folks at Prismier a call if you need some advice. We’ll be happy to share our thoughts on the best way to get your precision sheet metal parts made quickly and cost-effectively.
If you'd like to know more, pick up the phone and call us at (630) 592-4515 or email us at sales@prismier.com. Or if you're ready for a quote, email quotes@prismier.com. We'll be happy to discuss your options.