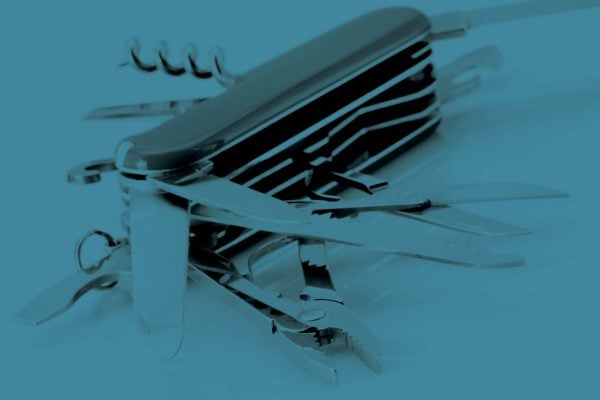
Quality
The Swiss Army Knife of Manufacturing
June 22, 2020
In our recent blog article, Materials Monday: The Allure of Aluminum, we discussed the wonderful, profoundly useful metal, aluminum. With a few exceptions, each of its many alloys is strong, lightweight, corrosion-resistant, and easily machined, formed, or stamped, and when anodized or powder-coated, aluminum is also quite aesthetic. While aluminum has long been a favorite of manufacturers and product designers, here we look at titanium, a strong contender for manufacturing projects that demand a high-performance material.
Although considered a lightweight material, it’s approximately two-thirds heavier by volume than aluminum. If this were a boxing match and you placed aluminum in the featherweight category, titanium would box alongside Rocky Balboa and Mr. T (although nowhere close to Ivan Drago). That said, titanium is roughly half the weight of steel but just as strong, and twice as strong as aluminum but only 60 percent heavier. The takeaway? Compared to other metals, product designers can use less titanium than either of the alternatives to get the job done.
Titanium’s other weakness, if you can call it that, is its relatively high cost. Although increased use throughout a range of industries has made titanium’s price tag more palatable, it still ranks among the most expensive of all “everyday” metals. Adding insult to injury, titanium is quite difficult to process and hard on the tooling used to machine and fabricate it, further driving up manufacturing costs. Despite this, titanium’s many attributes—when required—more than outweigh any price considerations.
An English clergyman and amateur geologist, Gregor had discovered the same metal four years earlier, albeit from a different ore. While splashing around in a stream near the village Manaccan in Cornwall, he came across some black, metallic sand, which he took back to his laboratory for chemical analysis. Gregor soon realized that he’d found a new metal, which he promptly named “menaccanite” after the nearby village. Long story short, Gregor’s name remains in the history books as the discoverer of titanium, but it was Klaproth’s name that stuck.
It’s not surprising that two people discovered titanium within a few years of one another. After all, it is the 4th most abundant engineering-grade metal on earth and ranks 9th among all the elements in the earth’s crust. The only reason titanium is not used more often and remains expensive is that it’s difficult to extract. It wasn’t until 1910 that the first chemically pure titanium was produced, when General Electric metallurgist Matthew Hunter heated titanium chloride (TiCl4) with sodium in a pressurized vessel. Another 22 years would pass until Wilhelm Kroll (another German scientist) would make large-scale production possible. Titanium had hit the big time.
Because of this affinity to its metal brethren, numerous titanium alloys exist. ASTM International provides dozens of titanium specifications, including B265, the Standard Specification for Titanium and Titanium Alloy Strip, Sheet, and Plate, which describes 41 distinct grades of strip, sheet, and plate, many alloyed with exotic minerals like palladium, cobalt, niobium, and vanadium, to name a few. Feel free to pick up a copy of B265 for a small fee, or just pick up the phone and call us here at Prismier to discuss your needs.
Manufacturing with titanium can be a bit tricky. We can tell you that welding must be performed in an inert atmosphere. Forming and bending can be troublesome as well due to titanium’s tendency to spring back under pressure. And as noted earlier, titanium is a real bear to cut, as any machinist or diemaker will attest. Still, these and other titanium manufacturing challenges are quite manageable given the right tooling and knowledgeable people.
As stated previously, there are plenty of other grades of titanium and plenty more to discuss. For one thing, there’s that whole alpha and beta phase thing we skimmed over just now, as well as the concept of H grades and similar minutiae, much of which is only of interest to material engineers and metallurgists. While we’re not going to do it here, you can reach out to us if you want to find out how titanium could solve your gnarly design problem.
If you'd like to know more, pick up the phone and call us at (630) 592-4515 or email us at sales@prismier.com. Or if you're ready for a quote, email quotes@prismier.com. We'll be happy to discuss your options.