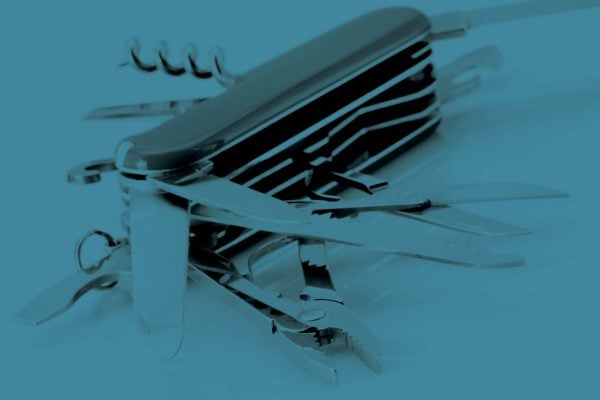
Quality
The Swiss Army Knife of Manufacturing
June 22, 2020
As mentioned in one of our previous blog posts, Materials Monday: The Big Picture, it was Englishman Henry Bessemer who is most often credited with inventing commercial steel production. And although the process has become far more efficient and cost-effective since that day in 1856, modern steelmaking isn’t all that different than in Bessemer’s time—it still requires a blast furnace, coal, limestone, and iron ore. But instead of blowing air through the molten iron, pure oxygen is used to lower its carbon content sufficiently to produce steel.
This is known as the basic oxygen process, or BOP. There is also electric arc furnace (EAF) and open-hearth (OHF) steelmaking, although the latter is largely obsolete. However the steel is made, though, it must then go through additional processing steps such as secondary refining, casting, shaping, and treating before it becomes usable to Prismier and other manufacturing companies. For further details, check out the interactive Steel Wheel on the Association for Iron and Steel Technology website.
Mild steels contain somewhere between 0.05–0.30 percent carbon (some manufacturers cap this at 0.24 percent). Regardless, they are very weldable, formable, and machinable. For instance, 1010 is a popular low-carbon steel containing 0.10 percent carbon (represented by the last two digits, or xx10). As is common with most carbon steels, there’s also roughly 0.50 percent manganese (but not to exceed 1.00 percent) along with trace amounts of sulfur and phosphorous. As a rule, mild steels cannot be hardened, although 1010 and others can be carburized, or heated in the presence of carbon to increase surface hardness.
Looking for good material for use in an automotive body panel, car bumper, or oil pan? How about bolts and fasteners, and high-volume, hardware-grade stamped metal components? Low carbon or mild steels are used in each of these instances due to their attractive price, malleability and ductility, widespread availability, and superior manufacturability.
The relative hardenability of these high carbon and ultra-high carbon steels edges into tool steel territory. For instance, the chisel set in your garage might be made of 1090 steel, as are many knife blades, although neither will have nowhere near the toughness of one made from D2 tool steel. Additional details on these important metals will come in a later edition of Materials Monday.
The rules change based on the type or family of steel (alloy steels are broken down into eight categories, 2xxx through 9xxx), but for carbon steels, a 10xx number means the plain carbon steel we’ve been discussing. An 11xx indicates that the steel has been resulfurized (making it easy to machine), and 12xx means it’s been both resulfurized and rephosphorized (easier yet to machine).
Taking that concept further, some of the mild steels have an L in the middle, as in 11L17 and 12L14, metals that any machinist will tell you, “Cut like butter.” The downside to all this is higher material cost, decreased ductility and impact resistance (meaning they are more brittle), and in the case of the two metals just mentioned, the presence of cancer-causing lead.
One alternative to leaded low carbon steels is the 15xx family of non-re-sulfurized, high-manganese carbon steels, which contain up to 1.65 percent manganese. They’re not nearly as free-machining but boast better mechanical characteristics, including strength and hardenability. Just as manganese helps humans form strong bones and connective tissues, it plays a crucial role in the strength of many metals.
Hot rolled is an apt description for steel that is pinched between two hard metal rollers at very high temperatures, typically over 1700°F. It can be wound into large coils or cut into bars or planks before cooling. Thanks to this process, it forms a slightly rough, scaly surface, has slightly rounded corners and edges, and is less expensive than its cold rolled counterpart. As it cools, it may shrink non-uniformly, resulting in less than perfect precision in the final size and shape. Hot rolled steel is often used for the I-beams and other forms of “angle iron” found in skyscrapers and bridges.
Cold rolled steel, on the other hand, starts out like hot rolled steel, but then receives additional processing in the mill. It’s squeezed at room temperatures between progressively tighter sets of rollers and flatteners, thus decreasing its thickness while improving mechanical strength and dimensional accuracy. Any steel sheet used to make computer cabinets, appliances, garage door openers, and gazillions of other “pretty” products is almost certainly cold rolled.
Actually, that “one last thing” statement from earlier is false. There’s lots more to know about steels and indeed about all metals. For example, we didn’t discuss HSLA (high-strength low-alloy) steels, which break the rules described earlier through the addition of elements such as copper, nickel, and vanadium. These versatile metals are strong yet formable and have therefore become the darling of many automakers. Nor did we discuss Young’s modulus, or drawing quality (DQ), or any of the countless ways that metals can be heat-treated. It’s a long list.
So stay tuned. We’ll continue plugging away with future Materials Monday installments, but if you can’t wait, you know where to find us. We’re always happy to discuss metals.
If you'd like to know more, pick up the phone and call us at (630) 592-4515 or email us at sales@prismier.com. Or if you're ready for a quote, email quotes@prismier.com. We'll be happy to discuss your options.