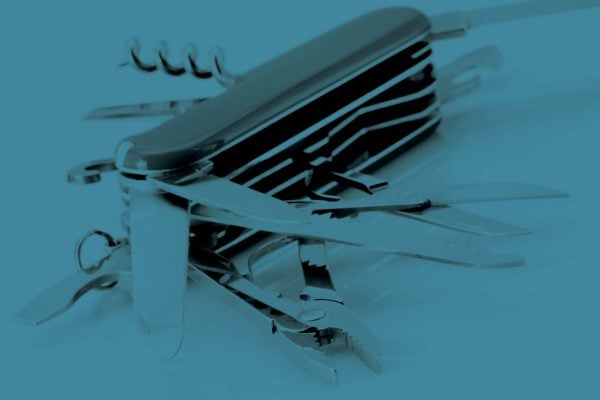
Quality
The Swiss Army Knife of Manufacturing
June 22, 2020
As you may recall in our introductory blog of this series, Materials Monday: The Big Picture, we offered a quick overview of the various metals used in manufactured components and why they are important. Here, we’ll chat a bit about the polymers used in manufacturing. You might know them as plastics.
With the plastics, as with metals, the varieties are numerous and the introductions just scratch the surface. There are far too many metals or plastics to cover in a single read—attempting to do so would be like writing the War and Peace of blog posts. As mentioned in the first blog post, we’ll delve more deeply on metals into the specifics of steel, aluminum, Inconel, and other alloys in future installments. Likewise, here we’ll lay the groundwork for upcoming Materials Monday installments featuring specific polymers in all their technical glory. So here goes.
Thermoset production is a lot like the chemical transformation that occurs when mixing a two-part epoxy. Like those superglues and garage floor coatings, thermosets are hard, often brittle, and generally quite heat-resistant. Most of the supposedly unbreakable dinnerware you might find at yard sales is made of melamine, a type of thermoset plastic. Fiberglass is a thermoset, as is the now-defunct Bakelite, the stuff of cheap cosmetic jewelry and old-fashioned rotary telephones (and is also the first entirely synthetic plastic, invented in 1907 by Belgian chemist Leo Baekeland).
We won’t talk too much about thermosets in future editions of Materials Monday. That’s because they cannot be remelted and are therefore impossible to recycle (more on this later). A safer and more earth-friendly alternative is thermoplastic. As you might have guessed just now, these versatile materials are extremely recyclable, found in everything from disposable water bottles and shampoo bottles to those cheap plastic lawn chairs that one shouldn’t stand on if you wish to avoid crashing to the ground. This sustainability feature is one of the primary reasons Prismier focuses almost exclusively on using thermoplastics these days.
Here again, distinct classes of thermoplastic exist, based largely on their internal structure. So-called amorphous thermoplastics such as polycarbonate (PC), polystyrene (PS), and acrylic are usually but not always translucent. As a rule, they bond well using the appropriate solvent or adhesive, are easy to thermoform (think plastic food containers), resistant to impact, sunlight, and liquids (though not chemicals), and are dimensionally stable. These properties make them an excellent choice for optical and lighting components, some medical applications, and a wide range of consumer products.
There are also semi-crystalline thermoplastics. These boast a more organized molecular structure than their amorphous cousins, and therefore exhibit greater strength, fatigue resistance, and are less prone to cracking. As with amorphous thermoplastics, it’s a big family, one that includes Nylon (PA), the ubiquitous polypropylene (PP) and polyethylenes (UHMW, HDPE, and LDPE), polyethylene terephthalate (PET), polybutylene terephthalate (PBT), polyphenylene sulfide (PPS), polytetrafluoroethylene (PTFE), polyether ether ketone (PEEK), and Acetal (POM), the latter two of which are extremely tough engineering-grade plastics.
Although some in the industry tend to lump all thermoplastics into one of these two groups, there’s another polymer subset worth mentioning. These are the thermoplastic elastomers (TPE), which include TPU (thermoplastic polyurethane), TPV (thermoplastic vulcanizates), and others. Each bears its own distinct properties and applications, but for now, know that the TPE family can range from rubberlike and transparent to very hard, rigid, and definitely not see-through. Their uses include footwear, gaskets, wire and cable insulation, and much more.
So are countless fillers and additives. For example, practically all polymers can (and often are) mixed with colorants during the plastic injection molding process (Legos are a great example). Fillers are also used to beef up or otherwise enhance many polymers. Where regular Nylon won’t cut the mustard, manufacturers will often fill it with glass fibers, greatly increasing its strength and hardness.
Similar tales can be told about metal fillers, flame retardants, UV stabilizers, antistatic compounds, and lubricants—all give polymers superpowers that otherwise would not exist, greatly expanding their capabilities and application range.
One final note on plastics. As suggested earlier, they’re everywhere; unfortunately, they’re also becoming a nuisance and perhaps even dangerous to human health (just Google microplastics if you don’t believe me). Yes, thermosets have their place, but designers should always aim for recyclable materials when possible. Consider your product’s lifespan and what will come after. Perhaps long after. And spread the good word about recycling. Your grandchildren will thank you. In the meantime, stay tuned for the lowdown on polymers and metals in upcoming editions of Materials Monday, and as always, give us a call or fire off an email if you’re wondering how they might fit into your next project.
If you'd like to know more, pick up the phone and call us at (630) 592-4515 or email us at sales@prismier.com. Or if you're ready for a quote, email quotes@prismier.com. We'll be happy to discuss your options.