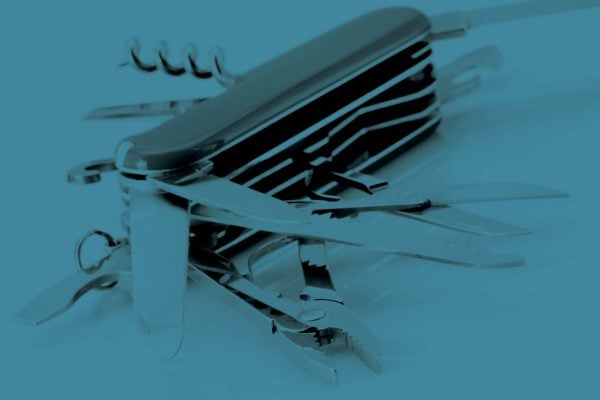
Quality
The Swiss Army Knife of Manufacturing
June 22, 2020
Choosing the right raw materials is a critical step in manufacturing a great product. Of course, you’ll consider pure metals and/or standard polymer classes of thermoplastic, thermoset, and thermoelastic materials. Whether using metals or plastics for your custom parts, there are also plenty of alloys or blends to consider. You’re probably already familiar with many of the metal alloys used throughout history. For example, millennia ago, metalworkers ushered in the Bronze Age when they discovered that adding small amounts of tin or zinc to their crucibles made copper much harder and stronger. Centuries later, some lazy blacksmith neglected to clean his furnace and realized that the bits of charcoal he’d left behind seemed to make the iron much more durable, thus creating the first steel. And far more recently, metallurgists learned that a smidgeon of chromium would make rusty old steel “stainless.” See our blogs Materials Monday: The Big Picture and Materials Monday: Polymers on Parade for our introductions to metal and plastic materials respectively.
It’s clear that alloying elements profoundly affect a metal’s physical properties and resulting performance, so it shouldn’t come as much of a surprise to learn that similar stories exist in the polymer world. In 1862, for instance, Alexander Parkes blended camphor and cellulose to make the notorious Parkesine, a material known for its highly flammable qualities. After this came Bakelite, a mix of phenol and formaldehyde, followed by polyethylene, polystyrene, and nylon, all derived from a witch’s brew of petrochemicals and various additives.
Today, the materials website MatWeb lists close to 100,000 polymers in its excellent online database. The Society of Plastics Engineers shows nearly as many, along with roughly half that number of additives and colorants. Long story short, there’s a polymer for practically every application imaginable, with more coming online daily. This Materials Monday will review some of the more common “alloying” elements, a.k.a. fillers and blends, used to construct this seeming universe of polymers, beginning with colorants.
Before leaving the fills and additive topic behind, bear in mind that there’s much more to this than the compounds and their various chemical compositions. For fills, at least, the shape, size, and concentration of the particles also play crucial roles. We already mentioned glass and carbon fiber, which are typically composed of individual strands but fills also come in spheres, cubes, flakes, and other geometric shapes. Smaller particles tend to improve strength more so than larger ones (but not always), just as the “more is better” principle does not always apply with fill concentration. Here again, reach out to an expert before traveling too far down the fills and additives path.
In most cases, the term “blending” refers to what we described earlier—incorporating various fillers, additives, and colorants into the pellet during the manufacturing process or immediately before injection molding. The latter relies on special machines that work much like the Kitchen Aid some of us keep under the counter for preparing weekend libations (albeit much more slowly) or via “dosing” devices that drop predetermined amounts of pellets into the hopper during the injection molding operation. At Prismier, we mold out of a wide variety of different thermoplastics using blends like PC/ABS and PPO/PS, as well as fillers like glass, carbon, ceramic, flame retardants, and UV absorbers. Our comprehensive plastic manufacturing services can help you choose the right raw materials and processes to take your product from design to delivery.
Finally, it’s important to note that everything discussed here refers to the pelletized feedstocks used in plastic injection molding. Many of these materials, though are also available in rod, sheet, and cast blocks suitable for CNC machining. Yes, these UV-resistant or glass-filled materials must be purchased that way—with the desired additives already included—but there’s certainly no shortage of them on the market. As always, give us a shout at Prismier if you want to explore further.
If you'd like to know more, pick up the phone and call us at (630) 592-4515 or email us at sales@prismier.com. Or if you're ready for a quote, email quotes@prismier.com. We'll be happy to discuss your options.