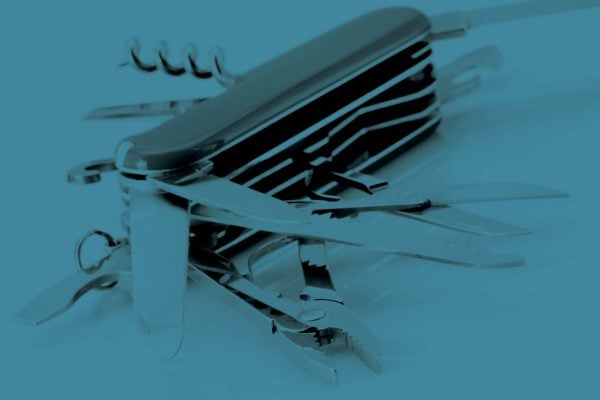
Quality
The Swiss Army Knife of Manufacturing
June 22, 2020
As noted in our earlier blog post, Materials Monday: Polymers on Parade, manufacturers have three broad polymer classes from which to choose for their product designs: thermosets, elastomers, and thermoplastics. This Materials Monday and the next will focus on the last and most common of these—thermoplastics—and their two subcategories, amorphous and semi-crystalline. We also have made additional resources available for each subcategory with our Amorphous Thermoplastics datasheet and our Semicrystalline Thermoplastics datasheet. You might also be interested in our blogs on injection molding which describe the processes of plastic injection molding and rapid injection molding.
Thermoplastics are popular for a multitude of reasons, chief among them the ability to use them over and over again. Properly recycled, the HDPE (high-density polyethylene) milk jug sitting in your refrigerator can easily be converted into next winter’s snowboard, and then into the picnic table you sit at the following summer to enjoy your barbeque dinner. In fact, HDPE can be recycled up to 10 times without compromising its quality. Most thermoplastics and many elastomers are equally recyclable.
On the contrary, amorphous thermoplastics are easily shaped and can be used to make rigid, durable structures. They also have some very definite and generally favorable characteristics. For instance, many are translucent. Because they allow light to pass through, amorphous thermoplastics enjoy widespread use in optical applications, and as relatively unbreakable windows and fish tanks. Before diving into all the other admirable properties and myriad roles for these ubiquitous thermoplastics, however, let’s invest a few sentences into what makes them “amorphous.”
At the risk of going all Scientific American on you, polymers are made of long strings of repeating molecules, or macromolecules. That’s where the term polymer came from, actually, since “poly” and “mer” are the Greek words for “many parts.” But where the molecules in semi-crystalline polymers sit next to one another in an orderly fashion like a box of spaghetti noodles, you can think of the molecules in amorphous polymers as cooked spaghetti on a plate, just waiting for your favorite pasta sauce (and special thanks to Encyclopedia Britannica for the spaghetti analogy).
Without further ado, let’s peek under the amorphous covers and see what polymers are available, where they might be found, and a little bit about what makes these essential materials tick:
ABS: Right out of the gate, we’re going to contradict ourselves on the “translucent” statement made previously. If you have a child or once were one, you’re almost certainly familiar with acrylonitrile butadiene styrene (ABS), the stuff of Legos. We’ll also backpedal on the whole chemical resistance thing, because ABS breaks the mold here as well. That’s why it’s common in sewer pipes and plumbing fittings (as is PVC, another amorphous thermoplastic). It’s low-cost, doesn’t peel, flake, or dissolve, and performs well at moderately high and low temperatures alike. It should not be left in direct sunlight for extended periods, though, and is generally not suitable for food applications. And like most plastics, ABS is quite nasty when exposed to direct flame and will actually catch fire, so take care around any source of spark or flame.
PMMA: Speaking of fish tanks, there’s acrylic, more commonly known as Plexiglas. Its technical name is poly (methyl methyl acrylate), or PMMA, a strong, scratch-resistant, and highly transparent example of amorphous thermoplastic. The Monterey Bay Aquarium in California, for example, uses 13-inch thick PMMA as the visitor-facing wall in one of its main exhibits. It’s also found in airplane windows, hockey rink barriers, see-through tabletops, and, as we’ve seen popping up in stores and restaurants everywhere over the past two years, sneeze guards. In the medical procedure known as keratoplasty, a piece of precision-molded acrylic replaces the cornea. This last example highlights acrylic’s extreme biocompatibility. It’s often suitable for dentures and bone implants, and has even earned the moniker “bone cement” for its use in orthopedic surgery. PMMA is also very moldable and can be mixed with colorants to make everything from cosmetic jewelry to smartphone housings.
PC: This is one instance where the term PC is welcome. Short for polycarbonate, PC is far stronger than PMMA but a bit less scratch-resistant, a smidge less transparent (88% vs. PMMA’s 92%), and significantly more expensive. Machine guarding and bank windows are constructed of PC, while bulletproof glass is made from sandwiched layers of polycarbonate and glass. Both are easy to machine, to join together using solvents and epoxies (super glue is one), and as with PMMA, PC is quite moldable. If yours is a medical application—especially one for use inside the human body—chances are good that PMMA will come out on top, although grades of PC specifically designed for this (PC-ISO, for example) are available. Otherwise, both of these amorphous thermoplastics offer good electrical and chemical resistance and are clear choices (pun intended) for many engineering-grade components.
PVC: If polymers were baseball, polyvinyl chloride (PVC) would be a switch-hitter. PVC competes with ABS pipe and fittings in the plumbing store, but can also be made clear like PMMA and PC. It comes in rigid or flexible grades, is sometimes food safe, and has flame retardant properties as well as excellent chemical and corrosion resistance, especially in its CPVC (chlorinated polyvinyl chloride) form. The electrical wiring running through your car is encased in PVC, as its underbody, while the mud flaps, door panels, and miscellaneous moldings are made of this omnipresent polymer. So are stadium roof coverings, the seats you sat on during the big game, and much of the guarding that the athletes wore. PVC is everywhere. However, the production, use, and disposal of PVC result in the release of toxic, chlorine-based chemicals which are building up in the water, air and food chain. Due to these negative environmental impacts, the use of this material has been on the steady decline in recent years.
PEI: Here’s another engineering-grade plastic. Polyetherimide (PEI) most commonly goes by the trade name Ultem, which as you might guess, is one tough thermoplastic. PEI boasts a unique combination of mechanical strength, thermal and electrical resistance, and is a favorite of the medical community for several reasons. The first is its resistance to hydrolysis in the face of steam and hot water and its ability to withstand repeated sterilization cycles in an autoclave or when subjected to gamma radiation. It’s also biocompatible and can be used in the food industry. Though not as strong or heat and impact resistant as PEEK (a semi-crystalline thermoplastic), it’s in the same family and is much less expensive. PEI has a nice amber color, is translucent but not see-through, and sees service in medical instruments, electrical connectors and insulators, components needed for semiconductor manufacturing, scientific instrument parts, and much more. Special attention needs to be paid when selecting this class of material as they are considered high temp which means the equipment and presses needed to work with this material must be able to operate at elevated molding temperatures.
Finally, toss in the word “filler” and many of the guidelines and properties just described go out the window. ABS can be made quite UV-resistant, for example, while fillers are often used to make PC and others more flame retardant. And practically all polymers can be made stronger with a little glass, metal, or fiber fill. In fact, one amorphous material can be combined with another. For example, PC and ABS are commonly combined in many applications. This mixture takes advantage of the strength of PC while reducing the overall cost as ABS is much less expensive than PC. Make a note that another of Prismier’s upcoming Manufacturing Simplified Blog articles will cover Blends and Fills in more detail. There are also thousands of polymer subcategories, trade names, and application-specific grades available, so keep looking if you’re not finding what you need. It’s almost certainly out there.
If you want to learn everything there is to know about these and other polymers, check out www.polymerdatabase.com (a very cool site). That, or just give us a call us here at Prismier. We’ve designed and manufactured plastic parts for years and can help steer you in the right direction on your next polymer project, amorphous or otherwise.
If you'd like to know more, pick up the phone and call us at (630) 592-4515 or email us at sales@prismier.com. Or if you're ready for a quote, email quotes@prismier.com. We'll be happy to discuss your options.