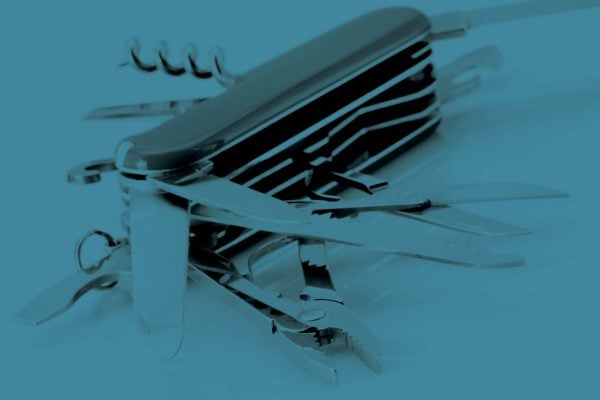
Quality
The Swiss Army Knife of Manufacturing
June 22, 2020
In fact, so crucial a role do lathes play in manufacturing that they were in large part responsible for the birth of the Industrial Revolution, after British mechanical engineer Henry Maudslay patented his screw-cutting lathe in 1799.
For those who’ve never seen one, a lathe is a machine tool that produces round or cylindrical parts. Easy, right? As you will soon see, however, this is a very general, slightly misleading statement. That’s because, like all CNC machinery, lathes grow a bit more capable each year, and can now perform operations and machine part geometries that were once only possible on milling machines.
For example, any lathe can whip up a set of candlesticks for your best friend’s upcoming birthday party. They can also turn shafts and pins, cut screw threads, and machine parts resembling soup cans and soda bottles. Only lathes with milling capabilities, though, can drill holes in the side of that soup can, or mill a series of decorative flats on said candlesticks. More on these mill-turn and multitasking lathes shortly.
A manual lathe, more commonly known as an engine lathe, toolroom lathe, and sometimes a chucker, accomplishes all this with a human operator. This skilled craftsperson must carefully turn the cranks on a set of graduated handwheels, guiding a series of turning tools, drills, and boring bars through whatever motions are needed to complete the workpiece.
CNC lathes eliminate this manual effort (though not the skill level) via precision servomotors that turn the ballscrew for each axis under an industrial computer’s digital guidance. Further, there’s no need to swap tools at each machining step like there is on a manual lathe. That’s because practically all CNC machinery comes with automatic tool-changing capabilities—on a lathe, this is most often achieved with an indexing, multi-station turret.
The third programming option is CAM software (CAM stands for Computer-Aided Manufacturing). Given the increasing complexity of today’s CNC lathes, which as already suggested, are getting more mill-like all the time, CAM software is the clear choice for shops that want to achieve greater efficiency and process control. CAM systems also support integration with toolpath simulation software and cloud-based tool libraries that help to streamline and safeguard the programming process.
Back to the different types of lathes. As mentioned previously, a basic two-axis CNC lathe has an X and Z axis, each driven by a computer-controlled servomotor. Most are also equipped with a movable tailstock, used to support longer workpieces (on manual lathes, the tailstock is often used to drill holes). A few decades ago, however, some clever machine tool designer decided to replace this movable tailstock with a rotating spindle, a.k.a. sub-spindle. This sub-spindle (on the right) sits directly opposite the main spindle (to the left), allowing both ends of a workpiece to be gripped simultaneously. It can also be used to grip the workpiece while machining its backside, eliminating the need for secondary operations.
Of course, these types of milling operations require precise control of the workpiece rotation. The lathe can no longer just spin the workpiece with reckless abandon, but must index and lock in exact positions, or rotate synchronously with the X or Z axis while a milling cutter removes material. This is known as a C-axis, and it significantly increases a lathe’s capabilities.
There is a downside to this mill-turn approach: tool capacity, or rather, lack thereof. A basic two-axis lathe typically carries eight to ten turning tools. Replace a few of these with the rotary tools needed to perform the milling operations just described and you might end up short on turning tools. The solution is a second turret, usually positioned opposite and below the main turret. The two-axis lathe has become a four-axis lathe, or even a six-axis lathe if equipped with C-axes on main and sub-spindle.
It’s also noteworthy how raw material gets loaded into a CNC lathe. As with its counterpart, the CNC machining center, lathes can accept sawed blanks and castings. These are typically loaded by hand, although given the shortage of skilled labor, robotic loading and unloading is becoming quite common. However they get in there, part blanks are usually gripped in a hydraulic or air-actuated chuck or collet device, while specially-designed fixtures can be used to hold on to non-round material and for secondary operations on milled parts.
Another option, one quite common in most turning departments, is the barfeeder. As the name implies, this well-known lathe accessory is used to feed a bar of raw material up to a couple of inches in diameter (depending on the size of the lathe) through the spindle tube and into the lathe’s work area, where it is clamped by the chuck. Once the part has been turned, a parting tool is used to cut off the finished workpiece, the bar of material is advances forward, and the process is repeated.
At the risk of leaving you hanging, that’s all we have time for in this installment of Learn Up. Hopefully, it was enough to pique your interest in CNC turning while giving you at least a basic understanding of its principles. In future editions, we’ll talk about the many types of cutting tools used on CNC lathes and machining centers, drills and taps, boring bars, threaders, groovers, and end mills among them, as well as complementary machining processes such as EDM and grinding. Until then, stay well.
If you'd like to know more, pick up the phone and call us at (630) 592-4515 or email us at sales@prismier.com. Or if you're ready for a quote, email quotes@prismier.com. We'll be happy to discuss your options.