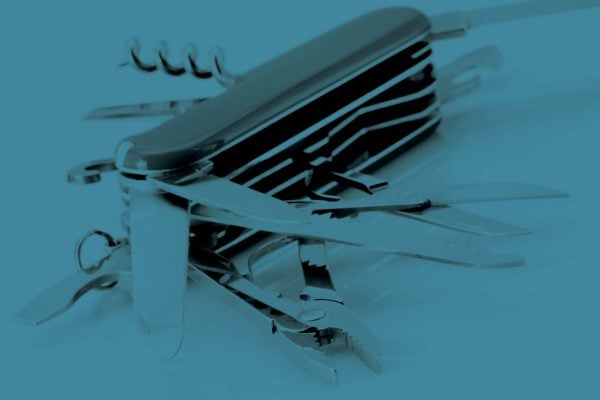
Quality
The Swiss Army Knife of Manufacturing
June 22, 2020
Precision sheet metal fabrication has an alter ego. It’s called CNC machining, a technology able to drill, mill, turn, grind, and erode rounds and bars of metal (and also plastic) into shapes that are often even more precise than their sheet metal-based counterparts. From the nuts and bolts that hold a child’s swing set together to the giant gears that open the Hoover Dam’s gates when it rains, machined parts are all around us.
CNC machining centers also have a rotating spindle, but here, the method of metal removal is reversed—the cutting tool spins while the workpiece is held securely in place. Machinists call this milling, even though machining centers also perform operations such as drilling, tapping, and slotting. And not to confuse anyone, but these and other operations can now be performed on multitasking lathes and turn-mill centers, blurring the lines between mill and lathe—more on this in a future post.
Consider the family car or truck. The engine and its many components were produced from cast, forged, or saw-cut hunks of steel and aluminum using various types of CNC machinery. So were the axles, brakes, wheels, and transmission housing. Due to the extreme production volumes found in the automotive world, many of the machine tools used to make these parts are highly-specialized and extremely automated. However, most share a common mechanism with the lower-volume, general-purpose CNC machine tools we’re about to discuss: a rotating spindle or spindles.
One of the most common CNC machine tools is the three-axis vertical machining center, or VMC. As with any milling machine, the workpiece is secured to the table using a vise, chuck, collet, clamp, and occasionally, double-backed tape (you’ll want to make sure the door stays closed in this last example). The table is then made to move side to side (the X-axis) or in and out (the Y-axis) while the spindle and its rotating cutting tool moves up and down in—you guessed it—the Z-axis.
All of these motions are executed by extremely accurate and powerful servomotors (one for each axis) that are given instructions by the machine’s computer, or simply “the control.” This is where the CNC part of the story comes in. CNC is an acronym for computerized numerical control, and as with any computer, it requires a software program to operate. In CNC-land, this is typically G-code, although some CNC machines can be programmed conversationally, using a now five decades-old language called APT (short for automatically programmed tool).
As its name implies, G-code is composed of commands such as G00 (rapid positioning) or G01 (linear interpolation), followed by X, Y, and Z coordinates. There are also M-codes for machine functions, F-codes for feedrates, and so on. Machinists most often generate G-code via the shop’s CAM software, although manual programming is also a possibility.
The scenario just described is possible using aftermarket accessories and is a relatively low-cost way for three-axis machine owners to decrease the number of operations needed to complete certain parts. And assuming the machine’s computer can control all five axes simultaneously, it opens the door to more complex work like propellers, turbine blades, and a replacement for Grandma’s worn-out hip.
That said, a far more elegant and accurate option exists. At the risk of sounding like Captain Obvious, it’s called a five-axis machining center. Most are equipped with vertical spindles, just like their three-axis cousins, although horizontal versions are also available. Whatever the orientation, five-axis machining centers are rapidly becoming the go-to machine tool for the work just described and more.
Most HMCs are also equipped with a rotary table and automatic pallet changer (APC). With this arrangement, a machinist can mount a tombstone—a big square block of cast iron—to the table, then clamp multiple workpieces to each of its four (or more) sides. And thanks to the APC, the tombstone and its machined occupants can be quickly swapped out for a fresh batch of workpiece blanks, providing for uninterrupted machining.
Of course, there are similar pallet systems available for practically any machining center, horizontal or otherwise. Some can even service multiple machine tools at once, a configuration known as a flexible manufacturing system (FMS), which usually comes with its own controller and scheduling system to keep each machine tool operating at peak efficiency. And even without an FMS, manufacturers often utilize robots to move raw material into a machining center and finished parts out, a trend that continues to gain traction given the shortage of skilled labor in the United States and elsewhere.
This brief description of milling technology pays short shrift to all the other moving pieces needed to operate a machine shop. There are the cutting tools to consider, the toolholders and workholding devices, never mind the software and other accessories found in any machine shop. We’ll cover all of it in future editions of Learn Up, starting with the next in this series: CNC lathes. Stay tuned.
If you'd like to know more, pick up the phone and call us at (630) 592-4515 or email us at sales@prismier.com. Or if you're ready for a quote, email quotes@prismier.com. We'll be happy to discuss your options.