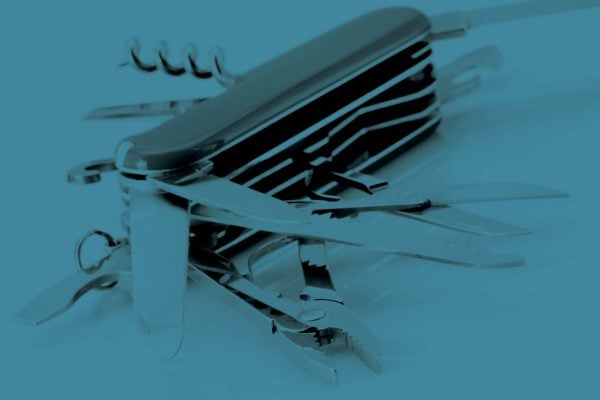
Quality
The Swiss Army Knife of Manufacturing
June 22, 2020
Manufacturing technology is terribly cool, but it doesn’t mean squat without modern metals, plastics, and composites.
Precision sheet metal fabrication. CNC milling and turning. Plastic injection molding. Die casting, additive manufacturing and electromechanical assembly. These are just a few of the manufacturing processes that quite literally keep the wheels on the big bus of society turning. But as with baking a cake or building a birdhouse, it all starts with the raw materials, which in the context of manufacturing means metals, polymers (a fancy name for plastic), and composites like Kevlar and fiberglass.
Without them, automakers couldn’t make cars and trucks. Fishing boat manufacturers would leave us casting our lines from shore, while orthopedic surgeons would tell their patients to take some Advil and stay off their bad knees. There’d be no refrigerators to keep the beer cold, no toothbrushes with which to maintain good oral hygiene. Without modern metals and plastic, we’d still be living in the Stone Age.
But what are these materials? Where do they come from and how are they made? Most importantly, how do designers and engineers know which one to use for a given application? We’ll attempt to answer these and other questions over the coming months, but we’ll have to ask you to be patient—there are an awful lot of different materials out there, each with their own unique properties. We’ll tackle them one by one and share them with you as quickly as possible.
Let’s start with an overview of metal. As any history buff will tell you, civilization’s rise hinged on metals such as iron and then steel. It’s no coincidence that major periods of humankind’s development are named after the metals they discovered and then used during that time. According to the Copper Development Association, humans first began using copper more than 11,000 years ago, although most historians suggest that the Copper Age didn’t actually begin until 5000 BC, followed by the Bronze Age and then the Iron Age.
The sequence of these eras also corresponds to the difficulty with which these metals can be worked. Back in the day, anyone with a strong arm and a little patience could stroll out to a nearby field, dig up a hunk of raw copper, and pound it into a dinner plate, or more likely, a weapon. This attribute of copper and other soft metals is known as malleability, an important property that we’ll explore in greater detail in future installments of Materials Monday.
Until then, it should be noted that bronze came along shortly afterward (in historical terms, anyway). Tired of seeing their copper weapons bashed to smithereens by rock-bearing hostiles, early metallurgists began experimenting with another discovery of that era-tin—and found that tossing a handful or two of this silvery element to the crucible would make copper much harder. The first alloy was born.
Iron is another important element. In fact, after oxygen, silicon, and aluminum, it is the most abundant element in the earth’s crust. Here again, though, iron is of little use in its pure form, as it is soft and ductile like copper. It is typically alloyed with small amounts of carbon and other elements, then pounded into shape while hot (wrought iron) or heated to the melting point and poured into a mold (cast iron).
We’ll dive into iron and its various forms more deeply in future posts, but before we leave the Iron Age, just know that iron eventually led to steel, the foundation of modern civilization. That’s because the right combination of iron ore, elements such as manganese and phosphorous, and a furnace hot enough and controllable enough to remove impurities creates an alloy that is much stronger and harder than plain old iron, namely steel.
Humans made steel throughout most of the so-called Iron Age, but the process was expensive, difficult, and somewhat unpredictable. It wasn’t until the 1850s that commercial steel production would become possible, when Englishman Henry Bessemer patented the invention that would give him a place in history—the Bessemer process.
Kudos or no, history also records that American inventor William Kelly and English metallurgist Robert Mushet (of Mushet Steel fame) each laid claim to the novel steelmaking process, suggesting that Bessemer stole their work. Controversy aside, the Bessemer process is now obsolete, replaced by electric arc furnaces able to make large quantities of high-quality steel more quickly and cost-effectively.
Steels are clearly important metals, and as you’ll see, a huge variety of them exist. From low-carbon and cold-rolled steels to stainless and tool steels, they’re used in everything from earth-moving equipment to children’s swing sets. However, there’s an equally important family of metals available, one whose primary element is number 13 on the periodic table: aluminum.
Where most steels are magnetic and subject to oxidation (excepting stainless steels), aluminum is neither. It’s also lighter than any steel, and boasts relatively high strength, making it a darling of aircraft manufacturers and cookware producers alike. Though more expensive than steel, aluminum and its many alloys make up for their higher cost with greater workability, corrosion resistance, and durability.
No discussion on metals would be complete without a brief mention of superalloys. Like stainless steel on steroids, metals such as Inconel, Hastelloy, and cobalt chrome alloy serve in critical functions across a range of industries. Most are heat-resistant, giving us the acronym HRSA (heat resistant super alloy). They’re also extremely tough and strong. Jet aircraft can’t fly without them. Gas and nuclear power plants would turn more slowly or not at all, and submarines would dive less deep. Superalloys are, quite simply, super.
There’s lots more. Magnesium and silver. Duplex steels. Titanium, nickel, and zinc. The list goes on. There are also numerous polymers to cover, something we’ll take a peek at in the next Materials Monday, after which we’ll take deep dives into the more important alloys, plastics, and composite materials. So, stay tuned, and if you have any questions in the meantime, drop us a line.
If you'd like to know more, pick up the phone and call us at (630) 592-4515 or email us at sales@prismier.com. Or if you're ready for a quote, email quotes@prismier.com. We'll be happy to discuss your options.