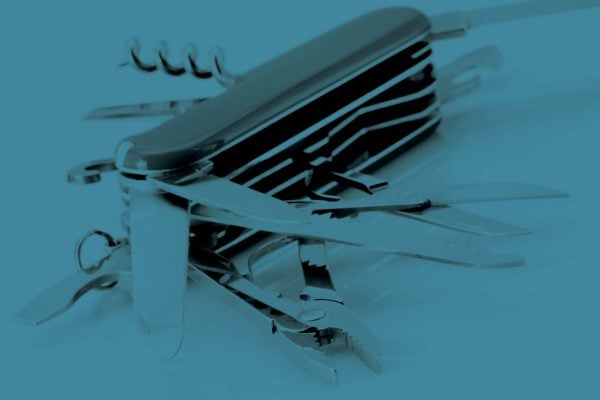
Quality
The Swiss Army Knife of Manufacturing
June 22, 2020
Stainless steel has been around a long time. American inventor and metallurgist Elwood Haynes applied for the first patent on “rustless steel” in 1912, although most industry experts credit Englishman Harry Brearley for the discovery during his search for a metal that would resist erosion in gun barrels. No matter, the two settled their differences and went on to form the litigious and long-defunct American Stainless Steel Corporation.
In all fairness, their work was nothing new. Even as far back as the 1700s, metallurgists recognized that adding small amounts of the element chromium to carbon steels and iron alloys made these metals stronger and more resistant to oxidation and chemical attack. As such, so-called “chromium steels” began to gain popularity over the next century, with steelmakers in Germany, Britain, and the U.S. jumping aboard the corrosion-resistant train. Some might argue that Haynes and Brearley were simply the beneficiaries of being in the right place at the right time.
As suggested earlier, much of this metal-speak is only of interest to metallurgists and materials engineers. For those of you designing tractor widgets or the next greatest medical device, what’s important is how the metal will perform in the field, and how much it will cost to machine, cut, form, stamp, and weld into its finished shape.
This is just the tip of the stainless steel iceberg. We didn’t delve too deeply into the duplex steel family, the ferritic stainless steels (which overlap with the others in the 400-series, most of which are martensitic), 200-series stainless (the stuff of sinks and spoons), and more. Nor did we mention that all of the superalloys—among them titanium, cobalt chrome, Inconel, Hastelloy, etc.—can be considered “stainless steels,” even though their exceptional toughness and heat-resistance puts them into another class entirely. Regardless, we’re happy to discuss all of these excellent materials and have years of experience turning each into beautiful and highly accurate custom parts. Just give us a call or get uploading.
If you'd like to know more, pick up the phone and call us at (630) 592-4515 or email us at sales@prismier.com. Or if you're ready for a quote, email quotes@prismier.com. We'll be happy to discuss your options.