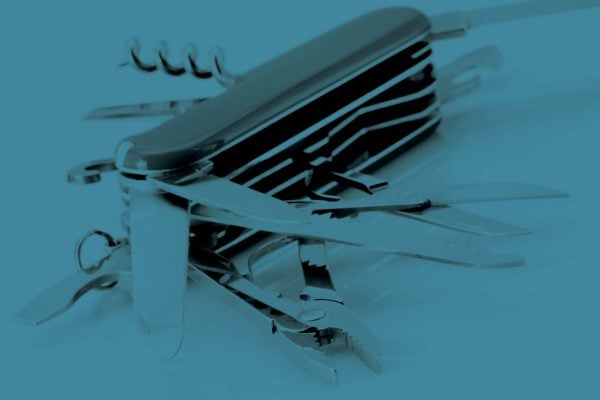
Quality
The Swiss Army Knife of Manufacturing
June 22, 2020
Fans of The Lord of the Rings might recall that Gandalf once advised Frodo, “All that is gold does not glitter.” Four decades after the book’s publication, the artist formerly known as Prince would borrow that phrase in his song “Gold”. Despite its widespread and timeless allure, however, not to mention its admirable physical and electrical properties, gold is too expensive for most industrial applications.
We’ll revisit this precious metal a bit later in this article, but now, let’s start with some other members of the red metal and yellow metal families. As you’ll see, these other metals—like gold and silver—are dense, corrosion resistant, and electrically conductive, making them an everyday and more affordable alternative to their more expensive counterparts.
Perhaps the most common of these is CDA 110, also known as electrolytic tough pitch (ETP) copper. It’s called an alloy, but being that it’s 99.9% pure copper, it barely qualifies. It’s very ductile, so can be worked into a wide variety of shapes, and forms an impervious film when exposed to the elements. This film eventually transforms into the beautiful blue-green patina seen on building facades and other structural elements such as that seen on The Statue of Liberty. Often used to make busbars for electric current power distribution, it can be formed as flat strips, solid bars, or rods, all of which are typically housed inside panel boards, busways and other enclosures.
Mix copper with zinc in a 60/40 ratio, toss in a trace amount of iron, and you have Muntz metal, known as the original yellow metal (never mind the fact that copper is reddish in color, rather than yellow, and is commonly referred to as a “red metal”). Invented by British metalworker George Frederick Muntz in 1832, his new alloy was a huge hit with shipbuilders, who used it as a cheaper but still effective replacement for the copper sheathing used to cover the hulls of sea-going ships. Today, Muntz metal is still found on ocean vessels in the form of fittings and pipes, although modern ships’ steel exteriors no longer require sheathing for protection.
Despite his success, Muntz’s development was nothing new. Not really. People had been mixing copper and zinc together for millennia; the old Brit just happened to stumble on the correct proportions of the two elements needed for his purposes, hitting a financial home run in the process. In fact, metallurgists will tell you that Muntz metal is but one of the many types of brass, an alloy that—like bronze—predates even ancient Egypt.
There’s also 260 brass, or cartridge brass, named so for its early use in ammunition cases. A 70/30 blend of copper and zinc, it is very formable, electrically conductive, and bears a distinct, shiny yellow appearance. Like most of the red and yellow metals, its copper content gives it the familiar corrosion-resistant patina mentioned earlier. Door hinges, name plates, electrical fixtures, and fasteners by the gazillions—these are just a few uses for this versatile metal.
There are a multitude of other types of brass with various molecular structures such as alpha brass, beta brass, and gamma brass. Just know that brass can be very soft and formable or hard and brittle, more suitable for casting and hot working. Either way, brass can be made into musical instruments, plumbing fixtures, marine components, hardware items, and much more.
Today, bronze remains a popular metal. Bronze bearings and bushings (from phosphor bronze or phos bronze) are commonly found in machinery of all kinds. Bronze propellers (made of nickel aluminum bronze) are used on boats and ships, while bronze lighting components and door and window hardware (white bronze) compete with those made of brass. And like our forbearers, we continue to pour molten bronze (which is 97% copper) into molds shaped like famous people, creating statues and other 3D art.
We’ve only touched the surface of red and yellow metals. Another important alloy is beryllium copper, a robust metal widely used in the telecommunications industry and known for its ability to be stamped into complex shapes with tight tolerances. Springs and load cells are made of beryllium copper, as are electronic connectors, cryogenic components, and thanks to its non-sparking qualities, hand tools for the oil and gas industry. Similarly, copper-nickel, also known as cupronickel, contains up to 49% nickel, making it very tough and wear-resistant. Nickels, dimes, quarters, and half-dollars are all made of cupronickel, as are heat exchangers and marine fasteners. And finally, nickel silver—used widely in the food and beverage industry for its strength and corrosion resistance—contains no silver at all but is instead made of copper, nickel, and zinc. It sees widespread use in heating coils, marine fittings, chemical equipment, and other applications requiring a durable yet malleable, corrosion resistant, and highly aesthetic metal. Additionally, nickel silver is commonly used for circuit board level shielding (BLS) for EMI or RF interference, as it is very solderable. At Prismier, we manufacture plenty of these shields and cans, along with the needed clips, contacts, discs, cages, and other precision micro parts, which you can read more about in our What is Rapid Micro Stamping? blog.
It’s this last factor—price—that makes it extremely unlikely you’ll be ordering any pure gold parts from Prismier or any other contract manufacturer, even though parts plated with gold are certainly an option. After all, NASA’s $10 billion James Webb telescope would have been impossible without the 100-nanometer thick (0.0000039″) layer of gold on its 18 mirror segments. In fact, just a few thousand bucks’ worth of gold plating is what gives this marvel of engineering the ability to see the earliest stars, which ironically is where gold and practically every other element in our universe first formed. Components made from many of the alloys mentioned above can be gold-plated to boost their protection from corrosion, heat, and wear and to help ensure a reliable electrical connection.
Let us know if you’re curious about red or yellow metals, or for that matter, any metal at all. We stamp, form, punch, cast, machine, and weld most of them and are happy to join in the conversation.
If you'd like to know more, pick up the phone and call us at (630) 592-4515 or email us at sales@prismier.com. Or if you're ready for a quote, email quotes@prismier.com. We'll be happy to discuss your options.