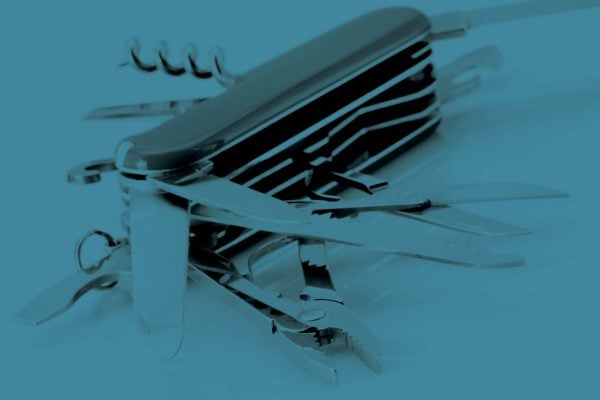
Quality
The Swiss Army Knife of Manufacturing
June 22, 2020
Happy with the price, quality, and delivery of your manufactured components, but not their appearance or durability? Here’s how to improve both.
From precision-machined motor shafts to micro-stamped electronic connectors, most manufactured parts need a little love after they’ve left the machine tool or production line. This might come in the form of a protective coating, a polishing operation, heat treatment to improve metallurgical properties, and/or dozens of other secondary processes.
These important finishing steps can add durability, aesthetic value, and often both to manufactured parts, and should not be overlooked during design and procurement activities. However, the different metals used in the production of these parts come with their own unique finishing requirements, which must be taken into consideration when deciding which process (or processes) to apply.
So what are these processes? Perhaps most importantly, how much do they add to the peice price, and time to the delivery? We’ll explore each in greater detail during future editions of Finishing Friday, but for now, here’s a quick overview to get you started:
There’s also vibratory finishing. The concept is the same, but instead of rolling parts around in a big can, they’re placed in an open container that, as its name implies, vibrates like crazy until the burrs fall away. Bead blasting is another common finishing process, as is straightlining (which uses abrasive to smooth parts), thermal deburring, electrochemical deburring, abrasive flow machining, and others; in a pinch, there’s always good old sandpaper.
We won’t go into the details here except to say that the passivating of stainless steels is a common way to enhance their corrosion resistance. Passivation is a type of conversion coating, which is not really a coating at all but rather a conversion of the metal’s surface to form the protective layer just described. Think of it as accelerated, highly-controlled rusting.
Multiple types of anodizing processes exist. Some are decorative and colorful (sulfuric acid anodizing), some are purely protective in nature (chromic acid anodizing), while still others can be made quite hard and, unlike most conversion coatings, relatively thick (aka, hard coat).
There’s also rhodium, gold, silver, tin…it’s a long list. The lion’s share of them are applied by placing the workpiece in a chemical stew and zapping it with some electrical current, although electroless and immersion plating is also common. And unlike conversion coating, dimensional buildup of the part surface can be expected, a factor that must be considered on tight-tolerance parts. More on all of this later.
When to use which? That’s a deep question. As we’ll discuss in more detail in an upcoming Finishing Friday, powder coating offers numerous advantages over painting. It provides a more durable finish, is more cost-effective on larger lot sizes, and is more eco-friendly than its VOC-filled counterpart wet paint. Powder coating equipment, however, is much more expensive than a basic paint line. Paint also offers more color choices than powder coat, and can more easily be color-matched. Though both are typically performed in a sealed booth, powdercoating requires curing in a large oven afterwards, an important consideration on heat sensitive parts.
Finally, it should be noted that not all finishes must be applied after the fact. For example, plastic injection molds can be textured with leather and wood-like surfaces. The parts coming out of these molds are thus improved aesthetically as well as functionally, with improved gripping surfaces or for overmolding reasons. Finishes for plastic parts is something we’ll discuss in a future post. Finishing Friday has a lot of ground to cover, so stay tuned. And if you can’t wait or have a question in the meantime, give us a call.
If you'd like to know more, pick up the phone and call us at (630) 592-4515 or email us at sales@prismier.com. Or if you're ready for a quote, email quotes@prismier.com. We'll be happy to discuss your options.