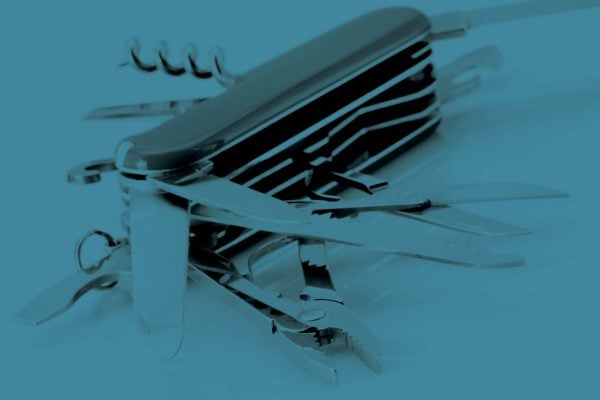
Quality
The Swiss Army Knife of Manufacturing
June 22, 2020
Burrs and sharp edges are unwanted but unavoidable side effects caused by many common manufacturing processes. Sharp edges, as you could probably guess, are the borders of any cut regions, and even when they may not appear to be very sharp, they can actually be razor sharp. Burrs are also sharp, but rather than the edge itself, they are little spikes or protrusions sticking up from the cut edge.
More than just unwanted, burrs and sharp edges are serious safety hazards that must be removed, or deburred, for a number of reasons. First and foremost, they are dangerous to people and other objects. They can quickly and quietly cut hands or any skin with which they come into contact. No one wants to create parts that cause injury, whether it’s to workers, customers, or anyone else. They can also damage adjacent objects. Second, they interfere with other finishing steps such as powder coating, paining, or plating. Your finished parts will have a much higher quality finish when deburred first. Finally, they can potentially affect fit and functionality by interfering with the mechanics of the part in a final assembly. Deburring is essential to ensure your parts can be properly assembled and your product function the way it was designed.
Now that you understand why deburring is important, let’s look at some of the common manufacturing processes that require this crucial task. Metalworking processes such as stamping, punching, machining, and laser cutting require this finishing step to clean up the inevitable burrs and sharp edges left behind. While welding doesn’t leave a burr, the joined edge typically requires some cleanup afterward. Heck, even 3D-printed parts need some loving attention once they’ve left the build platform.
Fortunately, there’s no shortage of ways to remove sharp edges and make precision parts safe, smooth, and beautiful. Whether it’s hitting them with sandpaper, blasting them with dry ice, or hooking them up to a million-dollar machine that shoves pressurized abrasive goo through a workpiece’s interior nooks and crannies, smoothing them as it passes, manufacturers have plenty of options. We’ll address many of the options available to you, depending on your material, production volume, and budget, as well as size and location of the burrs and sharp edges, so you can decide which process or processes are suitable for your project. Here goes:
If you'd like to know more, pick up the phone and call us at (630) 592-4515 or email us at sales@prismier.com. Or if you're ready for a quote, email quotes@prismier.com. We'll be happy to discuss your options.