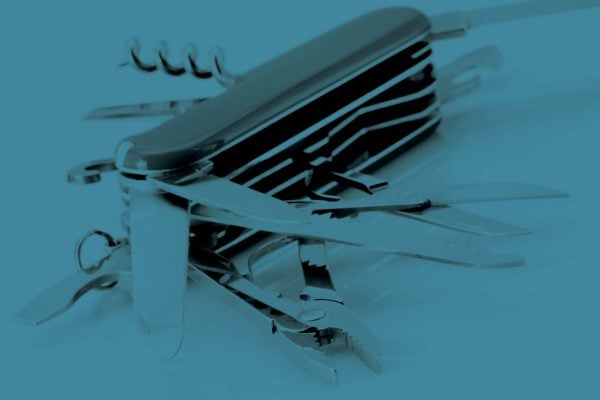
Quality
The Swiss Army Knife of Manufacturing
June 22, 2020
Depending on the material and application, however, there’s an alternative. It’s known as conversion coating. You can think of it as controlled rust. And while it can and often does stand alone, it is typically applied either before or after the plating, painting, and powder coating processes just mentioned, increasing their toughness, adherence, corrosion resistance, and/or electrical conductivity.
Conversion coating works by dunking metal parts into a chemical-filled tank. This might be a type of acid—citric and nitric acid are common—although caustic soda (lye) or electrolyte are also used. Electrical current is sometimes applied, in which case it’s referred to as electrochemical conversion coating. In either case, the end result is an extremely thin protective layer on the workpiece surface.
The same process occurs naturally with stainless steel (hence the name). The relatively high amounts of chromium in stainless steel alloys—between 10 to 30 percent—react with the oxygen in air to form chromium oxide, thus protecting the surface beneath. Aluminum is similarly corrosion resistant—due to its affinity for oxygen, it generates a thin layer of aluminum oxide, the stuff of sandpaper and ceramic. Compare each of these with cast iron and carbon steels, which gradually form that reddish, flaky nuisance known as iron oxide (Fe2O3), or rust. It never sleeps.
Conversion coating mimics these processes. It chemically or electrochemically “converts” the surface of ferrous and non-ferrous metals alike, leaving behind a hard, corrosion-resistant, and sometimes lubricious surface. Numerous types exist, among them:
As mentioned, conversion coating is robust enough to stand on its own, at least for some applications. However, it’s more likely to be used as a primer for paint and other coatings, or as a secondary finish over previously plated surfaces, enhancing their existing properties. In future installments of Finishing Friday, we’ll dig into the details of the various conversion coatings, among them the bluing and blackening of steels, chromate and “chem-film,” and the big Kahuna of all conversion coatings, anodizing. Stay tuned.
If you'd like to know more, pick up the phone and call us at (630) 592-4515 or email us at sales@prismier.com. Or if you're ready for a quote, email quotes@prismier.com. We'll be happy to discuss your options.